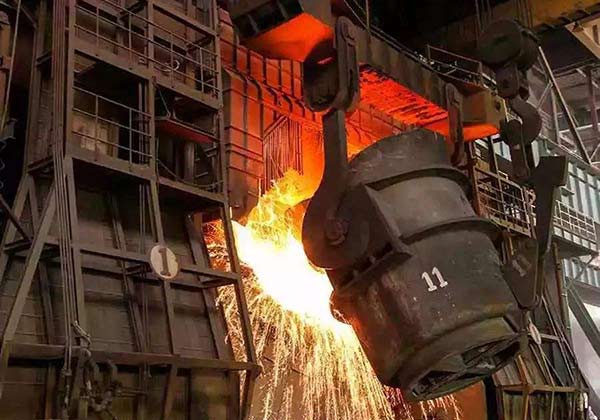
حول المغرفة
1. Main Use
A ladle refining furnace can be used for steel refining in primary furnaces (فرن القوس الكهربائي, فرن مسطح, محول), and is important metallurgical equipment to meet continuous casting and rolling.
2. Equipment Features
Equipment with atmospheric arc heating, vacuum degassing, blowing argon stirring, blowing oxygen feeding wire, atmospheric pressure or vacuum charging, temperature measurement, أخذ العينات, TV camera, frequency observation, and other functions.
The introduction of amorphous refractory casting construction technology
As a construction method for ladle bottom and ladle wall of amorphous refractories, the most common pouring construction method was introduced at first.
2.1 Pouring Construction
Pouring construction method
أولاً, natural maintenance is carried out for about half a day after the ladle bottom is constructed.
ثم, the frame and mixing mixer is installed, and after pouring the resistant material, to fill the entire gap evenly, a stick vibrator is used to help vibrate.
After about half a day of natural maintenance for demoulding, then the construction of refractory brick masonry is carried out for the slag line part.
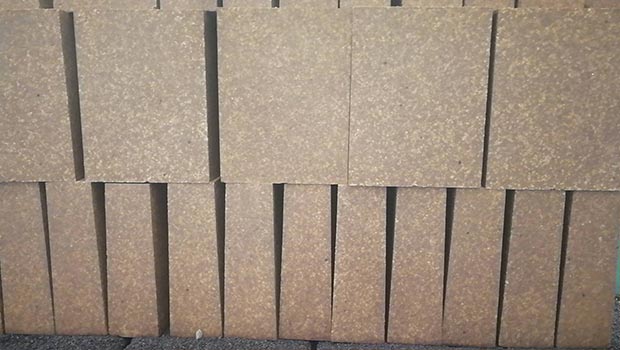
2.2 Selection Of Pouring Material
For the properties of refractory materials used in the bottom and wall of the package, it is required not only to have good corrosion and slag resistance but also to have a stable structure.
It is generally considered that magnesia-alumina refractory bricks are required to meet the above conditions.
When the amount of MgO in MgAl refractories is in the range of 7-28%, a dense and stable spinel solid solution is formed. لذلك, it is generally used as a refractory material for steelmaking ladles.
PER refractory plants attach importance to cost reduction, improvement of abrasion resistance in the steel impact section, and the effect of residual expansion and therefore use Magnesia Alumina refractory materials as castables.
فضلاً عن ذلك, even when the thickness of the long construction body is thin (يصل إلى 40 مم), the flowability of the castable is ensured.
لذلك, the particle size of Al2O3 aggregate was set at 8 mm or less, and metallic Al was added as a measure to prevent bursting during drying.
2.3 Results Of Practical Application
The rate of melt loss was investigated for the uppermost part of the ladle wall of a 15t ladle.
Compared to refractory bricks, the maximum rate of melt loss in all parts of the castable was 0.4 mm/furnace, while the repair cycle of the slagline bricks (عن 40 furnaces of steel) was carried out only when the melt loss of the bricks reached about 16 مم. هكذا, there is no adverse effect on the ladle life.
فضلاً عن ذلك, the working surface can be repaired after use by removing the adhering metal and cleaning the surface in several ways, as long as the working surface is not completely molten.
This reduces the amount of refractory material used in the construction of new spraying and reduces the waste bricks produced by the ladle by about 30%.
2.4 Expanding The Topic Of Definition Of Technology
Although it is known that the casting material has no problem in terms of durability, it is necessary to reduce the overall cost of the refractory. لكن, in order to reduce the overall cost of steelmaking refractories, it is necessary to expand the application of the information technology to other refractory bodies (على سبيل المثال, 25t ladles, VLF ladles, steel discharge chutes, إلخ.).
About PER Refractory Groups
الحراريات’ products are made of green, توفير الطاقة, and environment-friendly refractory materials.
We produce clay insulation bricks, طوب اكسيد الالمونيوم خفيف الوزن, طوب اكسيد الالمونيوم, طوب اكسيد الالمونيوم, طوب موليت متكلس, طوب المغنيسيا الملبد, magnesia alumina bricks, طوب الكربون, طوب السيليكا, طوب جوفاء الألومينا, طوب عالي الألومينا, الطوب من الطين, وغيرها من المنتجات. You can contact us at any time to get the price of refractory bricks below the market price.