Zirconium Silicate
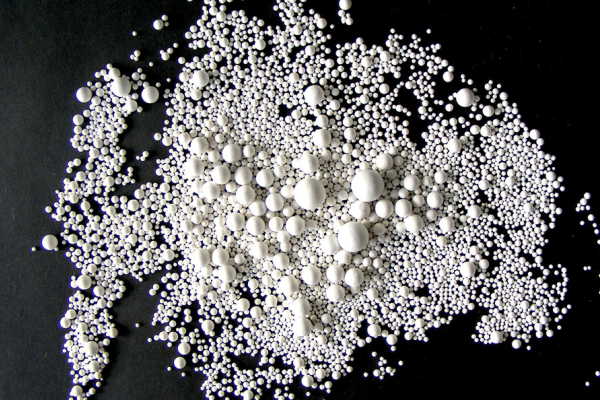
Zirconium silicate is a high-quality and inexpensive ceramic glaze emulsifier, mainly used in the production of color glaze for architectural ceramics, sanitary ceramics, daily ceramics, and electric porcelain, with fine particle size, good dispersion, strong covering power, good emulsification, good fluidity, etc. It has strong abrasion resistance and a whitening effect.
PER Refractories Factory offers high-quality zirconium silicate products. We have been engaged in supplying industrial refractories for a long time and have a good reputation among a wide range of customer groups, and we ensure the quality and consistency of our products. Contact us for a competitive price of zirconium silicate.
Properties of Zirconium Silicate
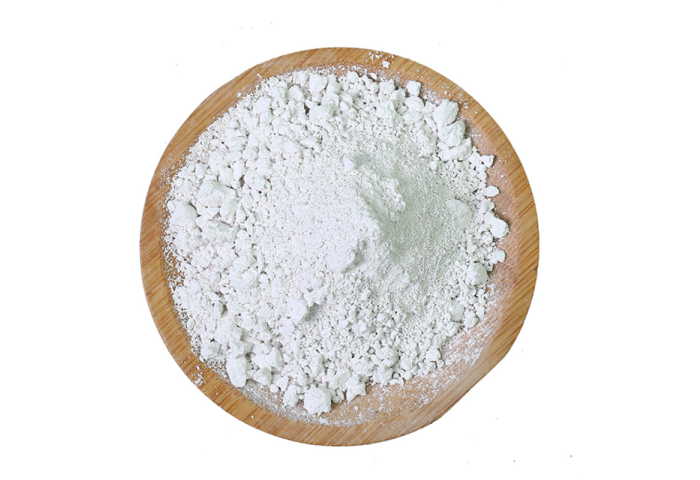
Products Description
Products Name: Zirconium Silicate
ZrO2+HfO2: 50%-65%
Specific Gravity: 4.69g/cm3
Fe2O3≤0.15
Tio2≤0.25
Refractive Index: 1.3-1.97
Zirconium Silicate is an odorless white or off-white powder. With a high refractive index of 1.93-2.01 and chemical stability performance, it is a high-quality and inexpensive emulsifier. It is widely used in the production of various architectural ceramics, sanitary ceramics, daily-use ceramics, first-class craft ceramics, etc. It is widely used in the processing and production of ceramic glazes and has a large application.
Zirconium silicate is also widely used in the production of ceramics because of its good chemical stability. It is therefore not affected by the firing atmosphere of ceramics, and it significantly improves the billet-glaze bonding properties and increases the hardness of ceramic glazes. Zirconium silicate is also further used in the production of color picture tubes in the television industry, emulsified glass in the glass industry, and enamel glazes for enamels.
Zirconium silicate has a high melting point: of 2,500 degrees Celsius, so it is also widely used in refractory materials, glass kiln zirconium tamping materials, pouring materials, and spray coatings.
When high-performance zirconium silicate has both whitening and stabilization conditions, it has better performance than conventional zirconium silicate in terms of zirconium silicate powder, particle morphology, particle size range, dispersion performance in media, and emulsion deflection after brick billet or glaze application.
The whitening effect of zirconium silicate is due to its formation of plagioclase, etc. after ceramic firing, which results in scattering of incident light waves, and this scattering is generally called large particle scattering or MieScattering.
Combining theoretical calculations and the actual situation of powder production, controlling the d50 value of high-performance zirconium silicate below 1.4um and d90 below 4.0um (based on the value measured by the Japanese laser particle analyzer) will produce the best emulsion whitening effect.
The concentrated particle size range is important in the whitening effect of zirconium silicate, and it is required to achieve as narrow a distribution of particles as possible during the grinding process of zirconium silicate.
Characteristics of Zirconium Silicate in Use
The results of the use of nano-scale zirconium silicate in the production of ceramics and functional materials show the following properties.
1. As an additive to ceramic glazes, zirconium silicate increases whiteness, strength, abrasion resistance, hydrolysis resistance, and corrosion resistance with decreasing particle size within a certain size range, increases self-cleaning ability, and reduces dosage.
2. Because of the strong resistance to hydrolysis of nanoscale zirconium silicate powder, it can be used as a carrier of nano-functional powder in an aqueous environment. For example, the nano-energy stone prepared by HeXiang Company uses nano-grade zirconium silicate as a carrier.
3. Due to its strong oxidation resistance, nanoscale zirconium silicate can be used as a surface coating agent for functional powders. For example, the red glaze of Chinese red ceramics is made of nanoscale zirconium silicate as a coating agent, and the color is red and bright without fading.
4. Because of its high strength and good wear resistance, nano-grade zirconium silicate powder is a high-quality raw material for grinding media and engineering ceramics.
The Role of Zirconium Silicate in Glaze
The role of zirconium silicate in ceramic glaze: In the process of making ceramics, many materials are used, and each of them plays a different role on the left and right. One of them is zirconium silicate, which is used frequently.
1. Zirconium silicate is a non-toxic, tasteless white or off-white powder, the raw material is natural high-purity zirconium sand concentrate, and then processed through ultra-fine grinding, iron removal, titanium processing, appearance modification disposal, etc. It is a good quality, inexpensive ceramic glaze emulsifier, whitening agent, anti-seepage agent, and stabilizer.
2. Zirconium silicate is widely used in the production of various architectural ceramics, sanitary ceramics, daily-use ceramics, and first-class craft ceramics, etc. Among them, it is widely used in the processing and production of ceramic glaze and is applied in large quantities. Because of its chemical stability, zirconium silicate is not affected by the firing atmosphere of ceramics, and it can improve the billet-glaze bonding properties of ceramics and increase the hardness of ceramic glazes.
3. Zirconium silicate can also play a whitening role in ceramic glazes, because zirconium silicate will constitute plagioclase, etc. after ceramic firing, which can constitute scattering of incident light waves, thus achieving emulsification and whitening.
4. This scattering is generally called large particle scattering or Mie scattering, and if the d50 value of high-performance zirconium silicate is controlled below 1.4um and the d90 value is controlled below 4.0um, then it will have a very good emulsion and whitening effect.
5. To achieve a better whitening effect of zirconium silicate, it is important to have a concentrated particle size range, so the grinding process of zirconium silicate should be as narrowly distributed as possible.
6. Zirconium silicate is also frequently used in the production of color picture tubes for the television industry, emulsified glass for the glass industry, and enamel for enamels. Zirconium silicate has a high melting point of about 2500 degrees Celsius, so it is also widely used in refractory materials, glass kiln zirconium mashing materials, pouring materials, and spray coatings.
Adding zirconium silicate to glaze not only can improve the billet-glaze separation performance of ceramics, and improve the hardness of ceramic glaze, but also can play a whitening role.
About PER Refractories Company
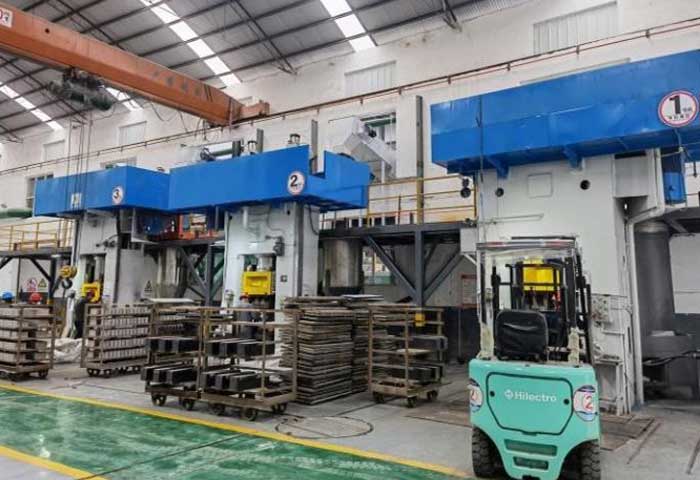
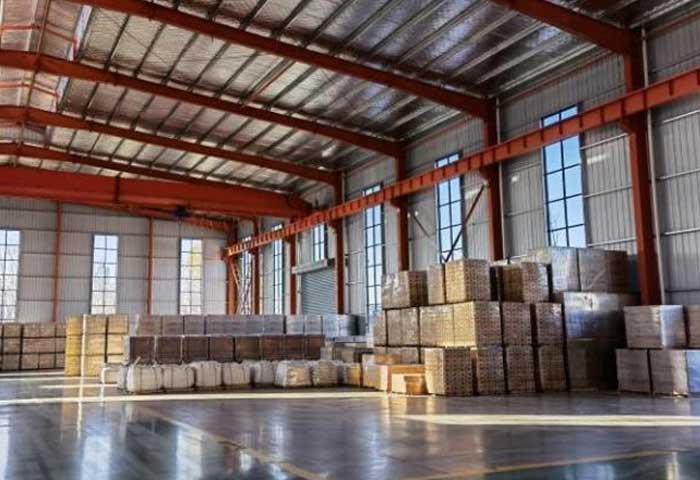
PER Refractories Company is located in Xinmi City, Henan Province, the hometown of refractory materials in China. Our company is a technology-based refractory enterprise integrating R&D, production, sales, and technical service. The rich resources and excellent quality in the territory provide unparalleled superior conditions for the production of refractory materials. Our main products are refractory clay bricks, high alumina refractory bricks, refractory silica bricks, magnesium refractory bricks, mullite bricks, insulation bricks, and other high-temperature resistant products.
Company PER refractory is the production base of green, energy-saving, and environment-friendly new refractory materials. Our company has passed ISO9001:2008 international quality system certification and GB/T24001-2004 / ISO14001:2004 environmental management system certification, enterprise-quality inspection agency certification. Our products are sold well in more than 20 countries all over the world. They are the preferred refractory products for metallurgy, non-ferrous, petrochemical, glass, ceramics, and other refractory industries.