Ladrillos de sílice
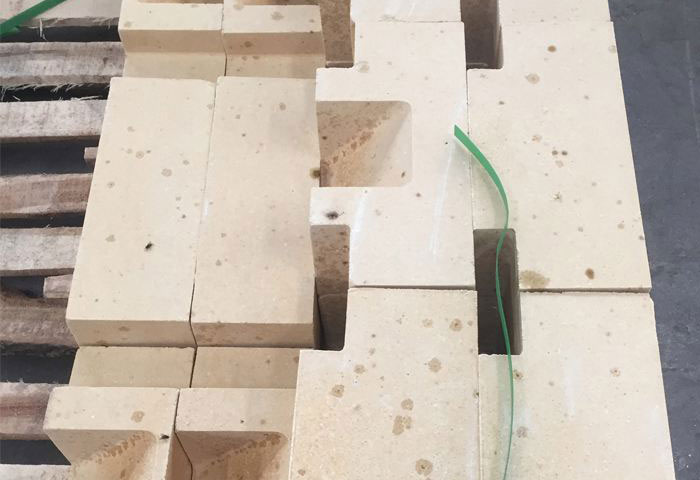
Ladrillos de sílice son un material refractario con sílice como ingrediente principal. Normalmente, El contenido de dióxido de silicio no es menor que 93%. Se puede arreglar o ser materiales refractarios.
PER refractario compañía, como ladrillos refractarios profesionales (Ladrillos refractarios de sílice) fabricante en China, puede ofrecerle un precio más bajo que el mercado. Contáctenos ahora para obtener el Última lista de precios de ladrillos refractarios de sílice.
Aplicaciones comunes de ladrillos de sílice
Ladrillos de fuego de sílice se utilizan principalmente para cámaras de carbonización de hornos y paredes de Coca -Cola de la sala de combustión, Sala de almacenamiento de calor de hornos planos de acero y sala de sedimentos, hornos calientes promedio, hornos de fusión de vidrio, y hornos de cerámica, como hornos y otras piezas de carga. También se usa para piezas de carga de alta temperatura y tapas de horno plano ácido del horno de aire caliente.
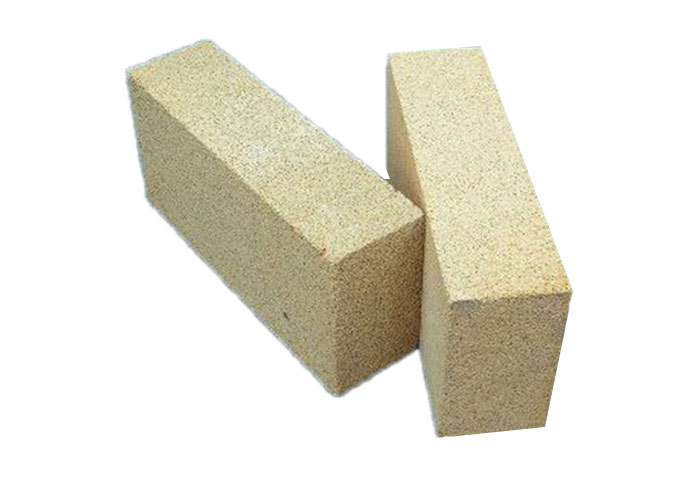
Aislamiento ligero de ladrillo de sílice
Ligeros aislantes ladrillos de sílice se utilizan principalmente para materiales de aislamiento térmico en hornos ácidos, como hornos de fusión y hornos de coque en la industria del vidrio.
Los ladrillos de sílice para hornos de aire caliente tienen las características de la expansión de la línea directa baja, Menos contenido de cuarzo residual, pequeña densidad, y puntos de ablandamiento de alta carga.
Y la apariencia es regular y el tamaño es preciso.
Se utiliza principalmente para áreas de alta temperatura, como el horno de aire caliente de alto horno, el cuerpo del horno superior, y la cuadrícula superior.
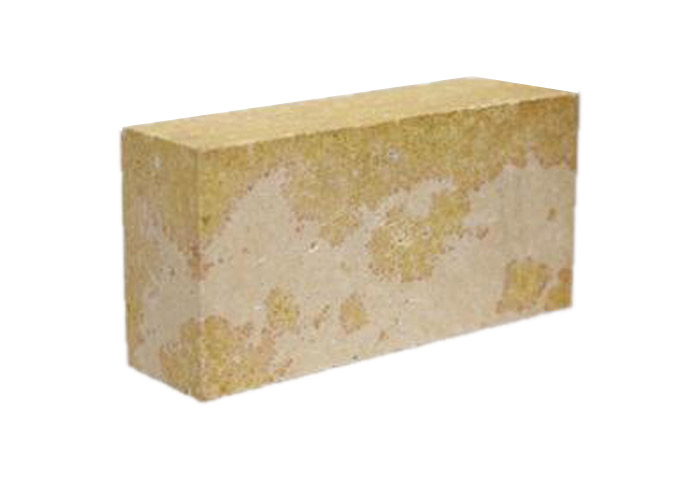
Ladrillo de sílice para horno de vidrio
Los ladrillos de sílice del horno de fusión de vidrio se utilizan principalmente para: El departamento de fusión y el departamento de trabajo del horno, paredes en el pecho y paredes delanteras y traseras, Tops de la sala de almacenamiento de calor, y paredes de partición superior de la sala de almacenamiento de calor.
El contenido de SiO2 de los ingredientes básicos y el rendimiento de los ladrillos de sílice es 96 ~ 98%.
Es un material fractivo con ácido. Su densidad es 2.35 a 2.38g/cm3.
Tiene una resistencia estructural de alta temperatura, como la alta temperatura de ablandamiento (1640 ~ 1700 ° C) y baja tasa de fluencia.
Y después de absorber algunos componentes alcalinos, Excepto por la erosión ligeramente ligeramente ligera, no reduce la fuerza de la estructura superior del horno. La principal desventaja de los ladrillos de sílice es la baja resistencia al calor sísmico.
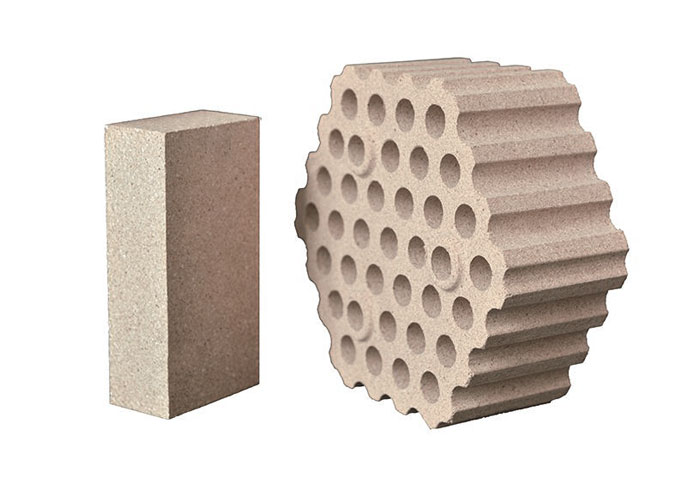
Ladrillo de sílice para el horno de aire caliente
Los ladrillos de sílice para hornos de aire caliente tienen las características de la expansión de la línea directa baja, Menos contenido de cuarzo residual, pequeña densidad, y puntos de ablandamiento de alta carga.
Y la apariencia es regular y el tamaño es preciso.
Se utiliza principalmente para áreas de alta temperatura, como el horno de aire caliente de alto horno, el cuerpo del horno superior, y la cuadrícula superior.
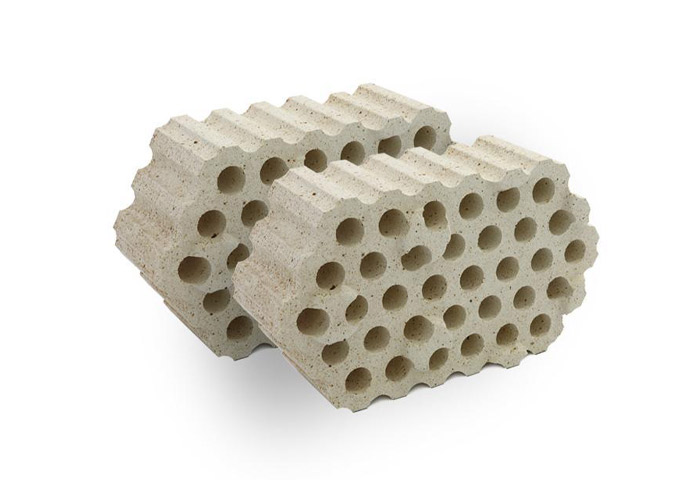
Ladrillo refractario especial
Ladrillo refractario de sílice de alta densidad de alta densidad
Aumentar la tasa de guía térmica de los ladrillos de sílice, acortar el tiempo de enfoque, y aumentar la productividad para tener un cierto efecto económico.
Por lo tanto, La fabricación de ladrillos de sílice de alta densidad y alta conducción ha atraído la atención de las personas.
La composición del ladrillo de fuego de silicato de alúmina es cristal (Sepa Ying, Cuarzo de colmillo, y cuarzo), fase de vidrio, y estómago.
Entre ellos, La fase de vidrio y el estómago son los principales factores para reducir la tasa de calentamiento térmico de los fogatas de silicio. Son los poros los que afectan los poros, seguido de la fase de vidrio.
Actualmente, La forma de aumentar la guía térmica de los ladrillos refractarios de sílice se obtiene principalmente aumentando el contenido de cuarzo escamoso y reduciendo los poros.
Índice físico y químico de ladrillos de sílice
Artículo | Ladrillo de sílice para horno de coque | Ladrillo de sílice para horno de vidrio | ||||
Cama de horno | otros | BG-96A | BG-96B | BG-95A | BG-95B | |
SiO2% ≥ | 94 | 96 | 96 | 95 | 95 | |
Fe2O3 %≥ | / | 0.8 | 1 | 1.2 | 1.2 | |
0.2MPA Rul ° C ≥ | 1650 | 1680 | 1670 | 1660 | 1650 | |
Fusión, sin embargo,: | / | / | / | |||
un ladrillo<20kg | 0.5 | 0.7 | ||||
un ladrillo ≥20 kg | 0.6 | |||||
Densidad verdadera g/cm3 ≤ | 2.34 | 2.35 | 2.34 | |||
SOCIEDAD ANÓNIMA % 1450° C × 2H | 0.2 | 0 | / | |||
AP % ≤ | 22(23) | 24 | 22(24) | |||
Expansión térmica 1000 ° C % ≤ | 1.28 | 1.3 | / | |||
CCS MPA ≥ | 30 | 25 | ||||
un ladrillo<20kg | 35(30) | |||||
un ladrillo ≥20 kg | 30(25) |
Características de los ladrillos de fuego de sílice
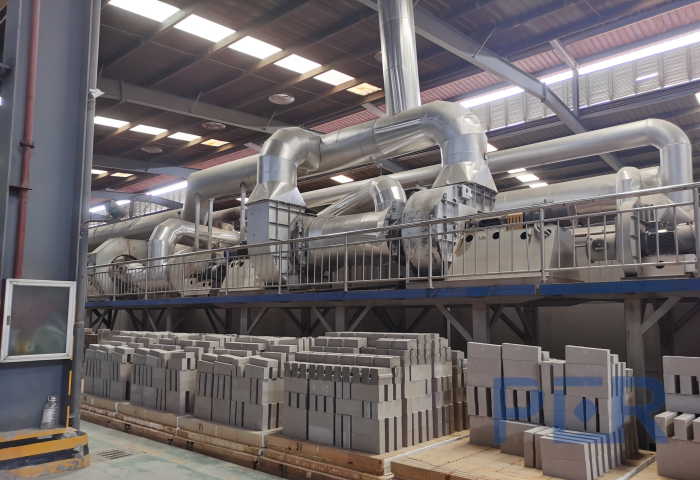
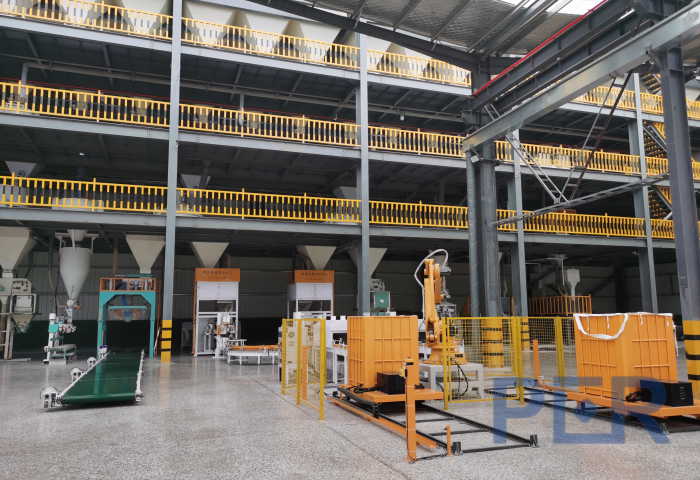
Por refractarios son una opción importante para una amplia gama de hornos resistentes a la temperatura alta.
La variedad principal son los ladrillos de fuego de sílice. Hervido por la sílice como materias primas hasta 1350 ~ 1 430 ℃. La fase principal de los ladrillos de sílice se transformará en cuarzo de ajuste, cuarzo cuadrado, y vidrio. La densidad real debe alcanzar 2.31 ~ 2.42 Gramos por centímetro cúbico.
Los ladrillos refractarios de sílice son materiales refractarios ácidos y tienen una buena capacidad de erosionar con resistencia al ácido. La temperatura de ablandamiento de la carga es tan alta como 1640 ~ 1670 ℃, y el volumen del uso a largo plazo a alta temperatura es relativamente estable. Tiene las ventajas de la conductividad térmica y el alto punto de ablandamiento, Fuerte capacidad de erosión de escoria anti-ácida.
Los ladrillos de fuego de sílice son principalmente materiales refractarios ácidos compuestos de cuarzo de ajuste, cuarzo cuadrado, y una pequeña cantidad de cuarzo y vidrio residuales.
El contenido de dióxido de silicio es más que 94%. Densidad real 2.35g/cm3. Tiene un rendimiento antierosión de escoria ácida.. Intensidad de alta temperatura. La temperatura de ablandamiento comienza la temperatura de 1620 ~ 1670 ° C. Utilizado a altas temperaturas durante mucho tiempo sin deformación. Bajo choque termal estabilidad (Se intercambia el calor de agua por 1 a 4 veces) con sílice natural como materias primas, Además de una cantidad apropiada de mineralizador para promover la transformación del cuarzo en el cuerpo en blanco en un lagarto. En la atmósfera restaurada, fue quemado lentamente 1350 ~ 1430 ° C. Al calentar a 1450 ° C, hay alrededor de 1.5 ~ 2.2� la acumulación general de hinchazón. Esta expansión residual se ajustará la costura y se asegurará de que la mampostería tenga una buena opresión de gas y resistencia estructural..
Características de ladrillos de sílice para horno de vidrio
Por refractarios tiene muchos años de experiencia en fabricación. Los ladrillos refractarios de sílice que producimos tienen muchas ventajas:
1. El volumen de alta temperatura es estable y no hará que el cuerpo del horno cambie debido a las fluctuaciones de temperatura: El horno de fusión de vidrio puede mantener el cuerpo del horno sin deformación en 1600 ° C, y la estructura es estable.
2. Contaminación leve de líquido de vidrio: El componente principal de la alta alúmina de ladrillo de sílice es SiO2. Si hay un bloque o un goteo de fusión durante el uso, no afectará la calidad del líquido de vidrio.
3. Erosión química: Los ladrillos refractarios de sílice de la estructura superior están erosionados por el R2O volatilizado de gas (metal alcalino) volátil en el material. Se genera una capa lisa de capa de deterioro en la superficie, bajar la velocidad de erosión y proteger el efecto.
4. Su densidad de volumen es pequeña: puede reducir el peso del cuerpo del horno. La materia prima formada en un ladrillo refractario de alúmina en síma es silicio. Cuanto mayor sea el contenido de SiO2 de las materias primas de silicio, Cuanto mayor sea la resistencia al fuego. Las impurezas muy dañinas son Al2O3, K2O, NA2O, etc., que reducen seriamente la resistencia refractaria de los productos refractarios.
Acerca de la compañía de refractarios PER
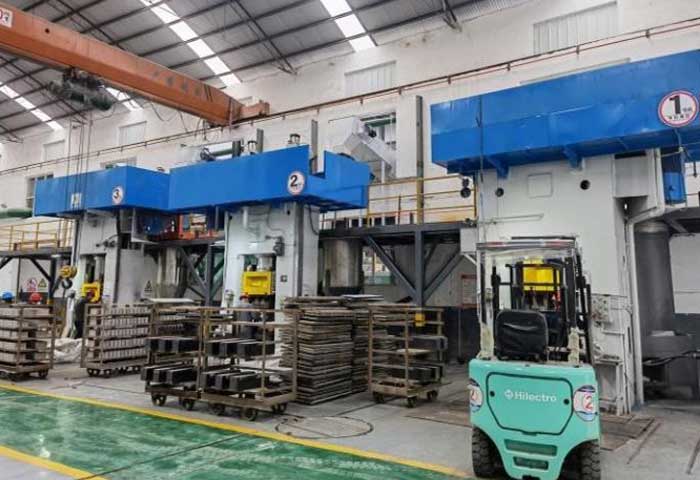
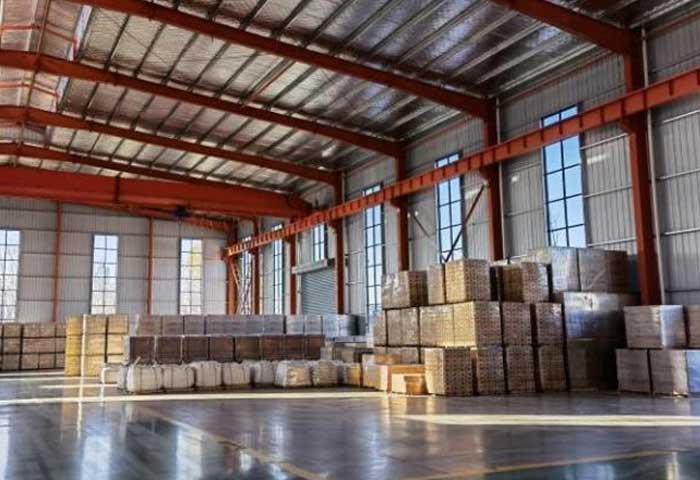
PER Refractories Company está ubicada en la ciudad de Xinmi, Provincia de Henan, la ciudad natal de los materiales refractarios en China. Nuestra empresa es una empresa refractaria basada en tecnología que integra R&D, producción, Ventas, y servicio tecnico. Los ricos recursos y la excelente calidad del territorio brindan condiciones superiores sin precedentes para la producción de materiales refractarios. Nuestros principales productos son ladrillos de arcilla refractaria, ladrillos refractarios con alto contenido de alúmina, ladrillos refractarios de sílice, ladrillos refractarios de magnesio, ladrillos de mullita, ladrillos aislantes, y otra productos resistentes a altas temperaturas.
Empresa PER refractario es la base de producción de verde, el ahorro de energía, y nuevos materiales refractarios respetuosos con el medio ambiente. Nuestra empresa ha pasado ISO9001:2008 certificación del sistema de calidad internacional y GB/T24001-2004 / ISO14001:2004 certificación del sistema de gestión ambiental, certificación de la agencia de inspección de calidad empresarial. Nuestros productos se venden bien en más de 20 países de todo el mundo. Son los productos refractarios preferidos para la metalurgia, no ferroso, petroquímico, vidrio, cerámica, y otras industrias refractarias.