AZS Refractory Bricks
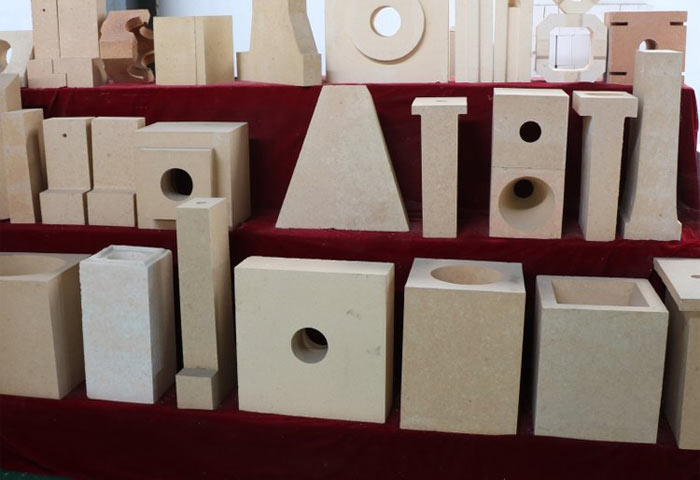
Nowadays, glass kilns have higher requirements for refractory bricks. High-quality refractory bricks can reduce cost consumption and produce better-quality products, and sintered AZS refractory bricks are widely used in glass kilns because of their anti-erosion and wear resistance.
Sintered AZS zirconium corundum brick is made of high-quality zirconium (ZrO2) bilang pangunahing hilaw na materyal, after scientific and reasonable grading, with excellent performance additives, by high-pressure molding, high-temperature sintering refractory products.
PER Refractories produces high-quality AZS fire bricks. You can always contact us for better AZS brick offers.
AZS Refractory Brick Characteristics
Its characteristics are high strength, high-temperature resistance, erosion resistance, and good chemical stability.
It is widely used in metallurgy, building materials, petroleum, industriya ng kemikal, Keramika, salamin, enamel, carbon black, mga metal na hindi ferrous, refractory materials, and other industries in industrial kilns.
Re-sintered zirconium corundum AZS sintered brick manufacturing process: the ZrO2 content in the zircon concentrate used to produce AZS sintered brick should be above 65%, and the combined TiO2, Fe2O3, and CaO should be less than 1%.
AZS Brick Physical and Chemical Performance Index Comparison
Name Brand | Zirconium mullite brick | Re-sintered electrofused AZS brick | High corundum brick | ||
Types | MZ-22 | MZ-30 | MZ-15 | AZS-32 | AZS-20 |
AL2O3% | ≥55 | ≥50 | ≥62 | ≥48 | ≥58 |
SiO2% | ≤25 | ≤22 | |||
ZrO2% | ≥22 | ≥30 | ≥15 | ≥32 | ≥18 |
Normal temperature compressive strength(Mpa) | ≥65 | ≥65 | ≥80 | ≥80 | |
Bulk density(g/cm3) | ≥2.85 | ≥2.95 | ≥2.70 | ≥3.25 | ≥2.80 |
0.2Mpa load softening temperature(T0.6%℃) | ≥1600 | ≥1600 | ≥1650 | ≥1625 | T2≥1650 |
Porosity(%) | ≤18 | ≤18 | ≤18 | ≤18 |
Characteristics Of Sintered AZS Bricks For Glass Kilns
1. Good erosion resistance.
2. Good wear resistance.
3. Good thermal shock performance at high temperatures.
Sintered AZS alumina fire bricks for glass kilns are generally used as the working layer of the glass kiln pool, which is in contact with the glass liquid and protects the kiln while resisting the erosion of the glass liquid. Kaya nga, sintered AZS bricks are mainly used in the glass kiln melting section of the chest wall and arch foot pool bottom sealing layer and other parts.
Physicochemical Index Of Sintered AZS Fire Bricks For Glass Kilns
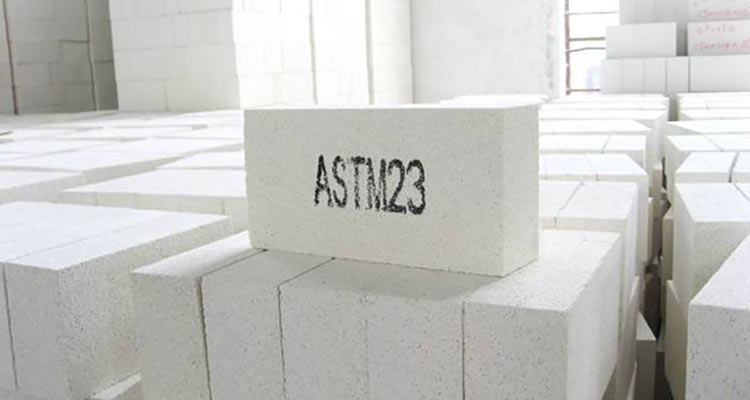
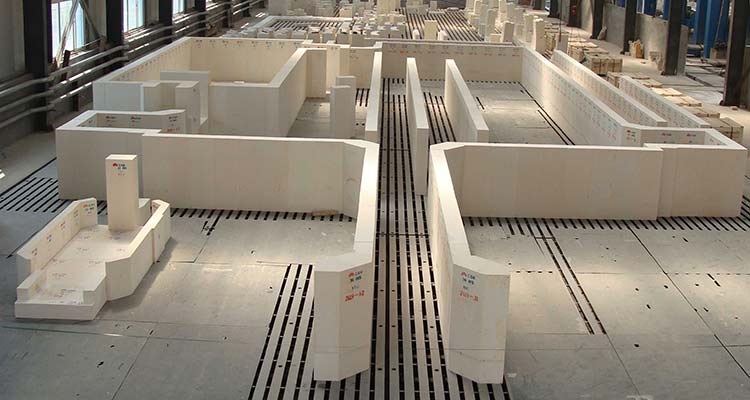
AZS Refractory Bricks/Electrofused Zirconium Corundum Bricks Used In Glass Kilns
Electrofused zirconium corundum bricks
AZS refractory bricks are called electrofused zirconium corundum bricks. It is made by melting the raw material completely and casting it in the casting mold, then cooling and solidifying it. It is mainly used in glass kilns. The shrinkage caused by volume shrinkage during the condensation process of this product is a matter to be noted when using it.
AZS refractory bricks are available in normal casting, inclined casting, non-cratering, and quasi-cratering, and can be cast in various ways to meet the requirements of ceramic frit furnaces, alkali furnaces, and glass furnaces. It is resistant to scouring, paglaban sa kaagnasan, and long service life, and is generally used in —– electrofusion oxidation method casting molding.
Three Important Driving Forces
AZS refractory brick change development has three important driving forces.
First glass manufacturers for less to maintain and usually need to change the quality of glass supply and demand.
The financial requirements of glass furnaces to make the kiln operating cycle longer.
And thirdly, the impact of the oxyfuel system.
These three requirements usually dictate the choice of modified refractory bricks when repairing the kiln.
These driving forces have also led glass manufacturers to choose modified refractory products for furnace care and maintenance and to invoke new skills for extensive repair work.
AZS Refractory Bricks Under Glass Refractory
Fused and cast aluminum bricks have established their application in this part of the melt pond roof, which is important for melting high-quality glass for oxyfuel pond furnace applications. Before the introduction of oxyfuel technology, only βˉ aluminum bricks were used in the top structure of the melting pool, and no fused cast aluminum bricks were used at the top of the melting pool.
Nowadays, no matter βˉ aluminum fusion casting products are used to produce a glittering film (screen cone), float glass, and borosilicate glass oxyfuel pool furnace part or all on the roof.
Fused cast AZS bricks can generally be used up to 1600°C or 1650°C (in glass products), while the roof of the furnace with electrically fused alumina bricks can operate very successfully at 1700°C. AZS refractory fire bricks, mataas na alumina brick, castables, square bricks, high-temperature mastic, high-temperature fireclay, acid-resistant bricks. It has a strong vitality in the use of glass kilns.
About PER Refractories Company
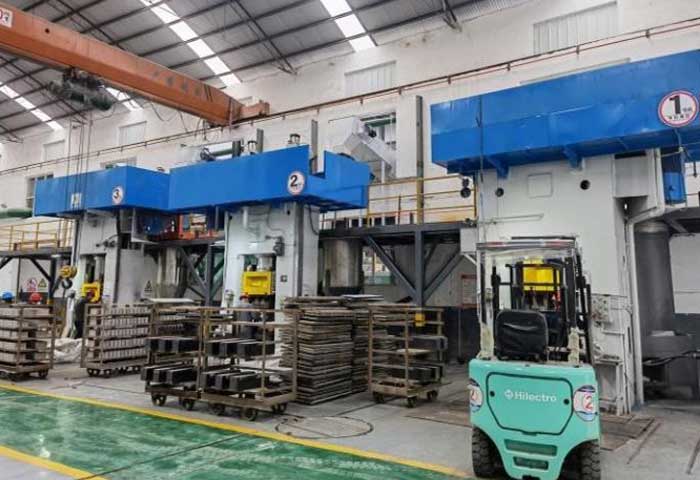
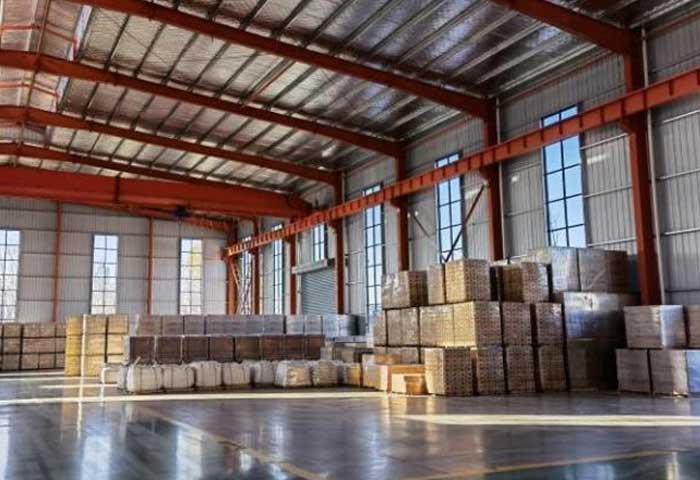
PER Refractories Company is located in Xinmi City, Lalawigan ng Henan, the hometown of refractory materials in China. Our company is a technology-based refractory enterprise integrating R&D, produksyon ng, mga benta, and technical service. The rich resources and excellent quality in the territory provide unparalleled superior conditions for the production of refractory materials. Our main products are refractory clay brick, mataas na alumina refractory brick, refractory silica brick, magnesium refractory bricks, mga brick ng mullite, mga brick ng pagkakabukod, and other high-temperature resistant products.
Company PER refractory is the production base of green, nakakatipid ng enerhiya, at kapaligiran friendly na mga bagong refractory materyales. Ang aming kumpanya ay pumasa sa ISO9001:2008 internasyonal na sistema ng kalidad ng sertipikasyon at GB / T24001-2004 / ISO14001:2004 sertipikasyon ng sistema ng pamamahala ng kapaligiran, Sertipikasyon ng Ahensya ng Inspeksyon na Kalidad ng Enterprise. Ang aming mga produkto ay ibinebenta nang maayos sa higit sa 20 mga bansa sa buong mundo. Sila ang ginustong mga produkto ng refractory para sa metalurhiya, di naman ferrous, petrochemical, salamin, Keramika, and other refractory industries.