Refractory Bricks For Sale
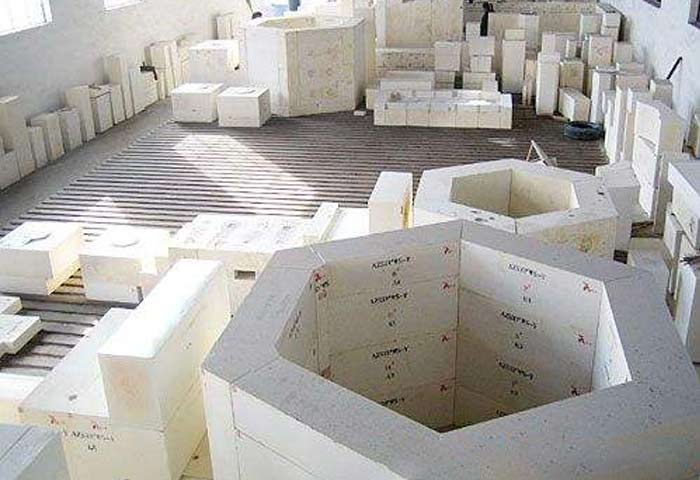
Refractory brick (fire brick) is a refractory material made of refractory clay or other refractory raw materials.
Refractory bricks (fire-resistant bricks) are mainly used as high-temperature building materials and structural materials for construction kilns and various thermal engineering equipment.
It can withstand various physical and chemical changes and mechanical effects at high temperatures.
According to the preparation process method divide can be divided into firing brick, not firing brick, capacitor turn (fusion casting brick), refractory insulation brick, atbp.
Tungkol sa PER Refractory Company
PER refractory company produces high-quality refractory bricks including refractory clay bricks, mataas na alumina refractory brick, refractory silica brick, magnesia refractory bricks, mga brick ng mullite, and insulation bricks, atbp.
Samantala, if you are interested in our refractory brick products, or if you are planning to build a furnace or kiln, you can contact us! We will reply to you promptly with professional advice and a competitive price!
Three Aspects Make Refractory Bricks Resistant to High Temperatures
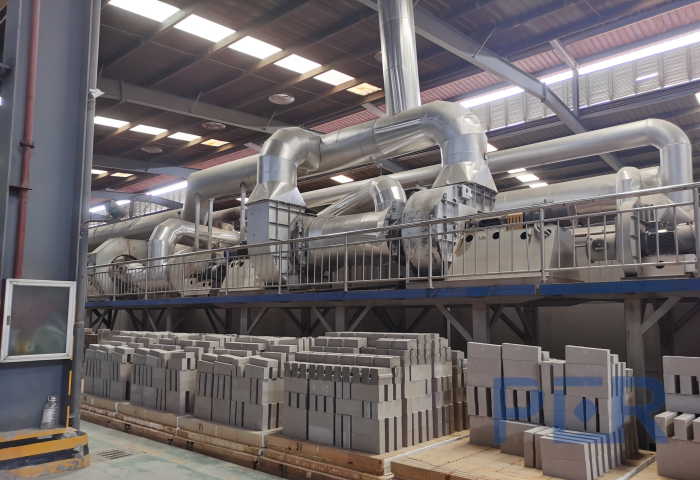
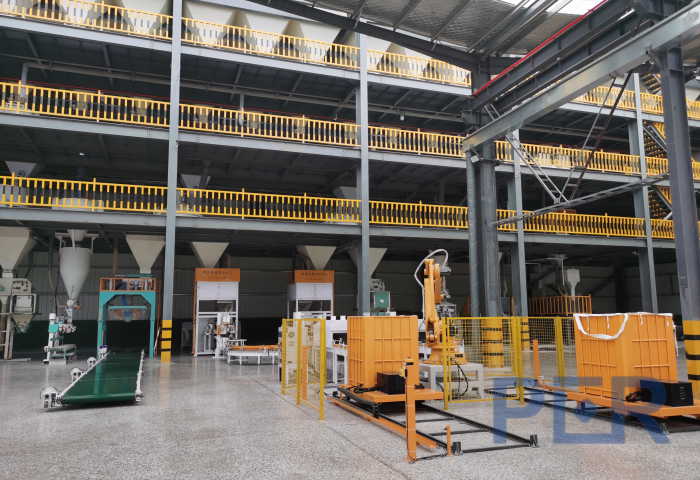
Summary of years of manufacturing experience of PER Refractory company: Reasons for high temperature resistance of refractory bricks.
1. The high refractoriness of the raw minerals used in refractory fire bricks.
2. As inorganic non-metallic materials from the level of raw materials determine the level of their use.
3. The finished billets are subjected to high temperatures above 1500°c in high-temperature tunnel kilns, so the refractory bricks can resist high temperatures and are suitable for high-temperature furnace linings.
The Most Complete Information About Refractory Brick Types
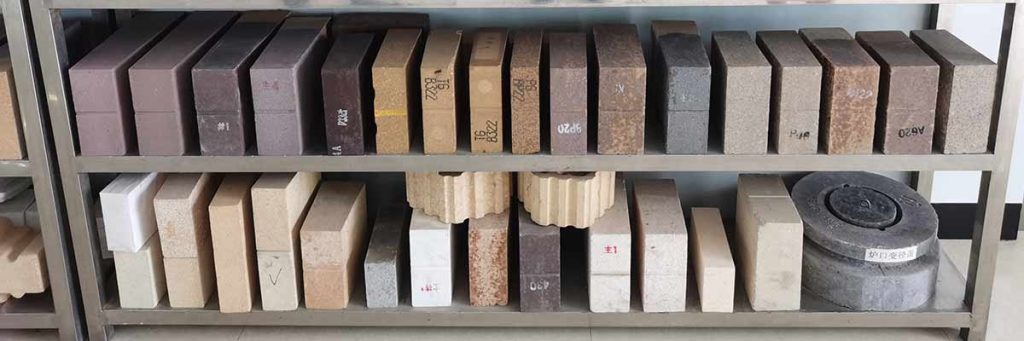
Refractory bricks can be classified into five major categories according to their composition: silica-alumina refractory bricks, alkaline series refractory bricks, carbon-containing refractory bricks, zirconium-containing refractory bricks, and thermal insulation refractory bricks. Any furnace is not just one kind of refractory bricks and masonry, need different refractory bricks with each other to use.
1. Silica-Alumina Refractory Bricks
Silica-aluminum refractory brick is based on the basic theory of the AL2O3-SiO2 binary system phase diagram, mainly including the following.
1.1 Mga brick ng Silica Refractory — It refers to the refractory brick containing SiO293% or more and is the main variety of acid refractory brick. It is mainly used for masonry coke ovens, but also used in a variety of glass, sets from, carbon calciner, the refractory brick of the vault, and other load-bearing parts of the hot work Mississippi Road. But it is not suitable for use in 600 ℃ and temperature fluctuations in thermal equipment.
1.2 Clay Refractory Bricks — Clay bricks mainly have mullite (25% sa 50%), glass phase (25% sa 60%), and square quartz and quartz (up to 30%) composed of. It is mainly used in blast furnaces, hot blast furnaces, heating furnaces, power boilers, lime kilns, mga rotary kiln, Keramika, and refractory brick firing kilns.
1.3 High Alumina Refractory Bricks — The mineral composition of high alumina bricks are corundum, mullite, and glass phase. Its content depends on the AL2O3/ SiO2 ratio and the type and amount of impurities. High alumina bricks products include fused cast bricks, fused granular bricks, unfired bricks, and unshaped refractory bricks. Mataas na alumina refractory brick ay malawakang ginagamit sa industriya ng bakal, non-ferrous metal industry, at iba pang mga industriya.
1.4 Corundum Refractory Bricks — Corundum brick refers to the AL2O3 content of not less than 90%, corundum as the main phase of refractory brick. It can be divided into sintered corundum bricks and electrofused corundum bricks. 2.
2. Alkaline Series Refractory Bricks
Alkaline refractory bricks are refractory products with alkaline oxides (Mg0 and CaO) as the main components. Its main varieties include the following.
2.1 Magnesia Refractory Bricks — magnesia brick is magnesite as raw material with magnesite as the main crystalline phase, MgO content in 80% sa 85% or more of the refractory brick. Its main products are Martin sand, ordinary metallurgical magnesium sand, ordinary magnesium brick, magnesium silicon brick, magnesium aluminum brick, magnesium calcium brick, magnesium carbon brick, and other varieties. Magnesia refractory brick is mainly used in flat furnaces, oxygen converters, electric furnaces, non-ferrous metal smelting, atbp.
2.2 Dolomite Bricks — Dolomite brick is a kind of alkaline refractory brick produced with dolomite as the main raw material. Widely used in the alkaline converter, also can be used for some refining lining of the package.
2.3 Magnesia Olivine Refractory Bricks — magnesia olivine refractory brick, is magnesia olivine 2MgO-SiO2 as the main component of a kind of refractory brick. Mainly used in flat furnace accumulation chamber lattice brick, brick for ingot casting, heating furnace bottom, and copper refining furnace also has a good use effect.
3. Carbon-Containing Refractory Bricks
Carbon-containing refractory bricks are made of carbon or carbon compounds. Its main varieties include the following.
3.1 Carbonaceous Refractory Bricks — Carbonaceous refractory brick is made of carbonaceous material as the main raw material, adding the right amount of binding agent made of high temperature resistant neutral refractory brick products. Carbonaceous refractory bricks are widely used in the electrochemical industry, industriya ng kemikal, industriya ng petrochemical, electroplating industry, ferroalloy industrial furnace, acid, alkali tank lining and pipeline, and furnace lining for smelting non-ferrous metals (such as lead, aluminyo, tin, atbp.).
3.2 Graphite Refractory Products — Graphite refractory products are made of natural graphite as raw material, with clay as binding agent refractory materials. One of the most produced and widely used is the graphite clay crucible for steel making and smelting non-ferrous metals.
3.3 Silicon Carbide Refractory Products — Silicon carbide refractory products are advanced refractory materials produced from silicon carbide (SiC) bilang hilaw na materyal. It has good wear resistance and corrosion resistance, high-temperature lightness, high thermal conductivity, small linear expansion coefficient, at magandang thermal shock resistance. In the chemical industry, it is mostly used in oil and gas generators, organic waste calciners, petroleum gasifiers, and desulfurization furnaces. In addition, in space technology, it can be used as a rocket nozzle and high-temperature gas turbine blade, atbp.
4. Zirconium-Containing Refractory Bricks
Zirconium-containing refractory bricks belong to a kind of acidic material. It is a product made of natural quartz sand (ZrSiO2) bilang hilaw na materyal.
Zirconium refractory bricks are different from silica-alumina refractory bricks and carbon-containing series refractory bricks, which have good slag resistance, and a small thermal expansion rate.
The thermal conductivity decreases with the increase of temperature, high load softening temperature, high abrasion strength, at magandang thermal shock resistance.
Now it has become an important material in various industrial fields. With the development of continuous casting and vacuum degassing technology in the metallurgical industry.
Zircon refractory bricks are more and more widely used, and there are mainly the following classifications.
4.1 Zircon Bricks — Zircon bricks are used in the steelmaking process, using the out-of-steel degassing method, and zircon refractory to molten slag, steel erosion resistance, and good resistance to thermal shock, and suitable for working under reduced pressure. Zirconia refractory bricks have high resistance to acidic slag and glass and are therefore also widely used in severely damaged parts of glass kilns where the most active glass is melted. Zircon refractories also have the property of not being penetrated by metallic aluminum, aluminum oxides, and their slag, and thus have also obtained good results in the furnace bottoms of aluminum refining.
4.2 AZS Electrofused Bricks — AZS electrofused brick, also known as electrofused zirconia corundum brick, with the development of the glass industry, AZS electrofused brick has become the key part of the glass kiln must refractory materials. It is more resistant to the erosion of glass liquid.
4.3 Zirconium Mullite Electrofusion Bricks — Zirconium mullite electrofusion brick, this kind of brick is characterized by a dense crystal structure, high load softening temperature, and good resistance to thermal shock. With high mechanical strength at room temperature and high temperature, good wear resistance, good thermal conductivity, and excellent resistance to slag erosion ability. The use of this kind of product is wide, used in metallurgical heating furnaces, even heat furnaces, calcium carbide furnace outlets, glass kiln walls, atbp., the use of very good results.
5. Heat-Insulating Refractory Bricks
Heat-insulating refractory bricks. It is a refractory material with high porosity, low bulk density, and low thermal conductivity. Heat-insulating refractories are also called light refractories. It includes the following classifications.
5.1 High Alumina Thermal Insulation Lightweight Refractory Bricks — High alumina thermal insulation lightweight refractory brick is a thermal insulation lightweight refractory brick with bauxite as the main AL2O3 content of not less than 48%. High alumina heat-insulating lightweight refractory bricks can be used for masonry heat insulation layer and no intense high-temperature molten material erosion and scouring effect of the parts. When in direct contact with the flame, the surface contact temperature of general high alumina thermal insulation refractory bricks shall not be higher than 1350℃. Mullite thermal insulation refractory bricks can be in direct contact with the flame and have the characteristics of high-temperature resistance, high strength, and remarkable energy-saving effect. It is suitable for the lining of pyrolysis furnaces, hot air furnaces, ceramic roller kilns, electric porcelain drawer kilns, and various resistance furnaces.
5.2 Clay Thermal Insulation Lightweight Refractory Bricks — clay thermal insulation lightweight refractory brick is made of refractory clay as the main raw material of AL2O3 content of 30% ~ 48% thermal insulation refractory brick. Its production process adopts the burn-out plus character method and foam method. Refractory clay, drift beads, and refractory clay clinker as raw materials, mixed with a binding agent and sawdust, after batching, mixing, pagmomolde, pagpapatayo ng mga, at pagpapaputok, to produce a bulk density of 0. 3 ~ 1. 5g/cm3 products. The production of clay thermal insulation bricks accounts for more than half of the total production of thermal insulation refractory bricks.
5.3 Diatomaceous Earth Thermal Insulation Lightweight Refractory Bricks — Diatomaceous earth thermal insulation lightweight refractory brick is a thermal insulation refractory product made of diatomaceous earth as the main raw material. It is mainly used in the heat insulation layer below 900℃.
5.4 Drift Bead Bricks—Drift bead brick, is a heat-insulating refractory product made of drift beads as the main raw material. Drift beads are hollow beads of aluminosilicate glass floated from fly ash of thermal power plants. It is a light, thin-walled, hollow, smooth surface, high-temperature resistant, and has good heat insulation performance. Using these excellent characteristics of drift beads, we can make light-weight thermal insulation refractory materials with excellent heat preservation performance. The production of drift bead brick can be semi-dry molding.
Performance of Refractory Bricks
Refractory fire brick is an inorganic non-metallic material with refractories not less than 1580℃, which is the basic material for serving high-temperature technology.
It is the structural material for masonry kilns and other thermal equipment.
It is also a functional material for manufacturing certain high-temperature containers and parts or playing a special role.
Refractory bricks must have a good organizational structure, thermal properties, mechanical properties, and use properties for successful use under the action of high temperature.
That is, there is a high degree of refractories, load softening temperature, thermal shock resistance, and resistance to chemical erosion and other properties.
Sa ganitong paraan, it can withstand the effects of various physical and chemical changes and meet the requirements of the use of thermal equipment and components.
About PER Refractories Company
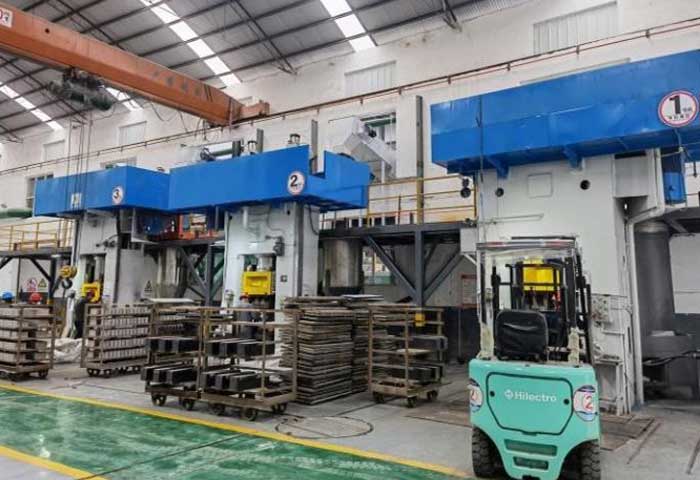
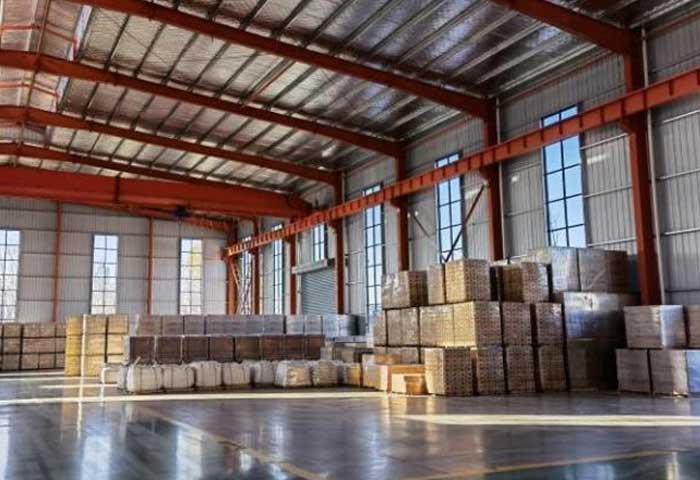
PER Refractories Company is located in Xinmi City, Lalawigan ng Henan, the hometown of refractory materials in China. Our company is a technology-based refractory enterprise integrating R&D, produksyon ng, mga benta, and technical service. The rich resources and excellent quality in the territory provide unparalleled superior conditions for the production of refractory materials. Our main products are refractory clay brick, mataas na alumina refractory brick, refractory silica brick, magnesium refractory bricks, mga brick ng mullite, mga brick ng pagkakabukod, and other high-temperature resistant products.
Company PER refractory is the production base of green, nakakatipid ng enerhiya, at kapaligiran friendly na mga bagong refractory materyales. Ang aming kumpanya ay pumasa sa ISO9001:2008 internasyonal na sistema ng kalidad ng sertipikasyon at GB / T24001-2004 / ISO14001:2004 sertipikasyon ng sistema ng pamamahala ng kapaligiran, Sertipikasyon ng Ahensya ng Inspeksyon na Kalidad ng Enterprise. Ang aming mga produkto ay ibinebenta nang maayos sa higit sa 20 mga bansa sa buong mundo. Sila ang ginustong mga produkto ng refractory para sa metalurhiya, di naman ferrous, petrochemical, salamin, Keramika, and other refractory industries.