
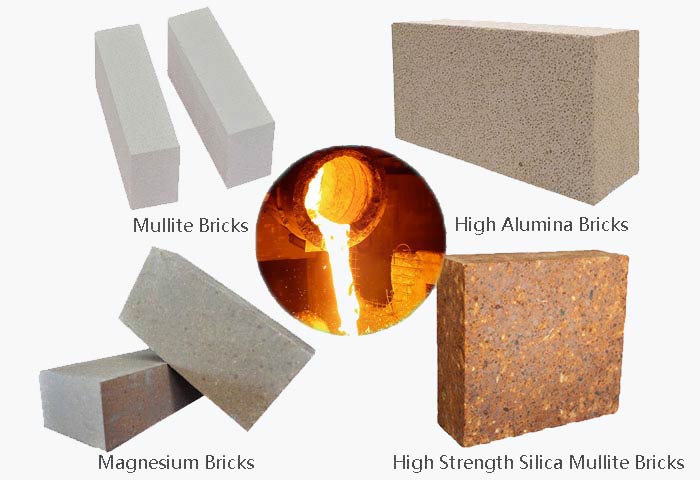
Firebricks for Sale
Refractory bricks are aluminosilicate fire refractory bricks with an AL2O3 content of 30% or more. Firebrick is a basic material for high-temperature technology and has a very close relationship with various industrial furnaces. Different kinds of refractory bricks also show different basic characteristics due to the differences in chemical mineral composition, microstructure, and production process.
PER refractory company produces high-quality refractory bricks including fire clay bricks, high alumina refractory fire bricks, silica fire bricks, magnesia fire bricks, mullite fire bricks, and insulation fire bricks, etc.
Meanwhile, if you are interested in our refractory firebrick products, or if you are planning to build a furnace or kiln, you can contact us! We will reply to you promptly with professional advice and a competitive price
Types Of Fire Bricks Products
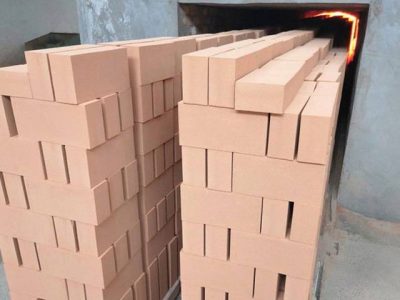
Fire Bricks
Our premium fire bricks are perfect for building fireplaces, ovens, and kilns. They are dense, heat-resistant, and designed to withstand extreme temperatures.
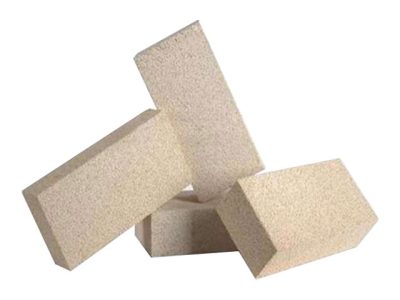
Insulating Bricks
Keep your furnaces and kilns energy-efficient and heat-up times reduced with our insulating bricks. They offer excellent thermal insulation properties and maintain thermal stability even at high temperatures.

Magnesia Bricks
Our magnesia-based bricks are ideal for high-temperature furnace linings, rotary kilns, and incinerators. They offer exceptional resistance to high heat, chemical erosion, and thermal shock.
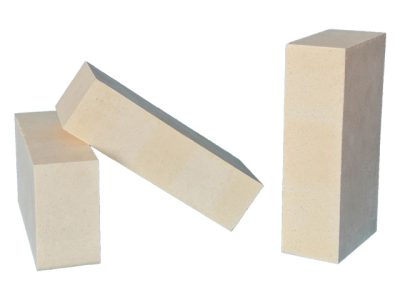
Mullite Bricks
Mullite bricks offer excellent thermal shock resistance, low thermal expansion, and great strength at high temperatures. They are often used in electrical and thermal insulation applications.
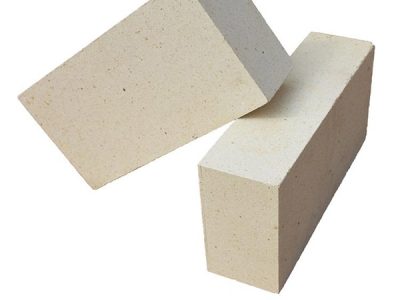
High Alumina Bricks
Our high alumina bricks are made from high-quality bauxite, and are perfect for high-temperature applications. They can withstand temperatures of up to 1780°C, are resistant to abrasion and wear, and have low thermal conductivity.
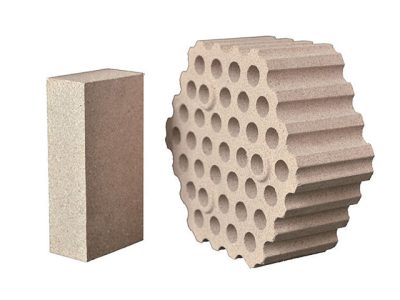
Silica Bricks
Our high-quality silica bricks are perfect for kiln linings, furnaces, and other high-temperature applications. They are highly durable, resistant to corrosion, and can withstand temperatures up to 1600°C.
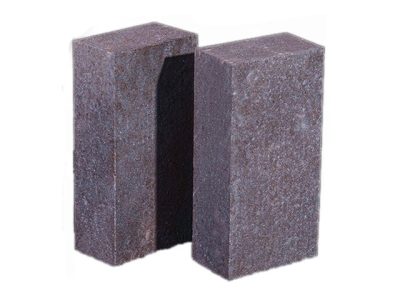
Chrome Bricks
Made from high-purity chromite ore, our chrome bricks are ideal for molten metal applications, such as in foundries and steel mills. They are highly abrasion-resistant, have low porosity, and offer excellent thermal stability.
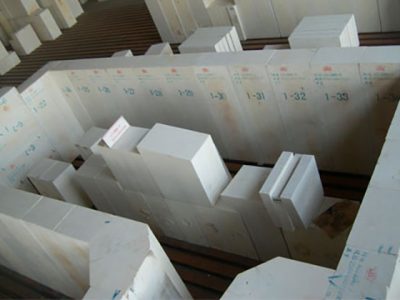
AZS Bricks
Our AZS bricks are made from a unique blend of high-grade raw materials and advanced manufacturing processes that ensure unparalleled durability, resilience and resistance to thermal shock, erosion and chemical attack.
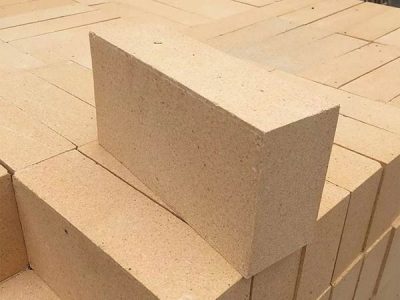
Clay Bricks
PER produces standard clay bricks and special clay bricks. The clay bricks we produce are suitable for glass kilns, ceramic kilns, rotary kilns and other industrial kilns. The operating temperature of standard clay bricks is 1250℃-1350℃.
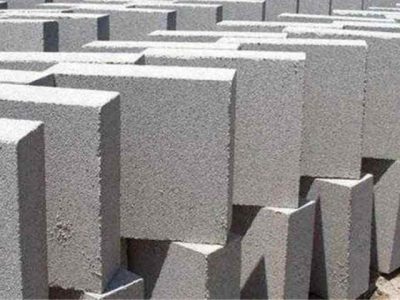
Lightweight Bricks
PER refractory brick manufacturer offers standard light weight bricks or customized refractory fire bricks. The products include lightweight clay bricks, lightweight silica bricks, lightweight mullite bricks, lightweight insulation bricks, etc.
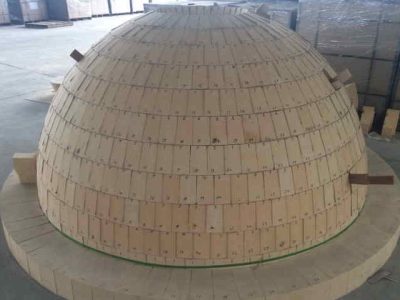
Kiln Fire Brick
We offer a variety of alkaline refractory bricks, acid refractory bricks, and neutral refractory bricks. Also, we can customize various kiln fire bricks on demand.
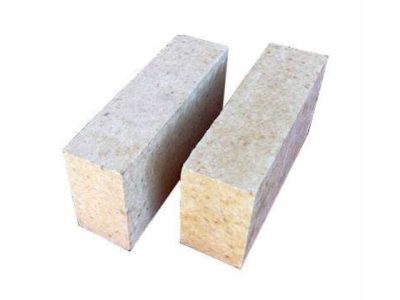
Andalusite Brick
PER's andalusite refractory bricks have good low thermal conductivity, high resistance to slagging and creep resistance. It can be used in hot blast furnace, hot blast tower, blast furnace and other key parts.
How The Fire Bricks are Packed?
PER Refractory Manufacturing Company has many years of experience in exporting refractory bricks:
The general fireproof brick packaging is divided into two ways: wooden pallet or straw rope.
1. Wooden pallet packaging is generally 1m×1m in length and width, and the base is 15cm, so how are the refractory bricks placed in the wooden pallet?
For example, the size of the standard brick is 230 * 114 * 65mm, four trips per layer vertical 15 of + horizontal 4 = 64.
According to the 3.4kg/block of clay bricks, it can be loaded with ten to twelve layers. Each pallet is packed according to the upper limit of 2.3 tons.
2. Straw rope packaging to standard brick as an example, generally 6 pieces packed together.
Refractory Brick Physical Chemical Function Reference
Firebrick’s basic quality requirements are alumina higher than 38% (usually 42-47%) as well as low iron and low alkali metal content, these should belong to its chemical properties.
But while you understand the physical properties like the specifications of fire bricks, don’t neglect to mention the physical and chemical properties of refractory bricks. Such properties include shaped refractory bricks, high alumina fire bricks for coke ovens, etc. will have.
As fire-resistant bricks are a kind of ultra-fine silica powder material formed by the condensation of SiO2 and Si gaseous state that occurs during metallurgy of ferrosilicon alloy and industrial silicon with the rapid oxygenation in oxygen.
Foremost, the appearance of fireproof bricks is a gray and white powder, with refractories > 1600 ℃. Its capacity: 200~250kg/m3.
Second, the precision of fire-resistant bricks, fire resistant bricks in the precision of less than 1 micron accounted for more than 80%, per capita particle size in 0.1 ~ 0.3 microns, specific surface area: 20 ~ 28m2 / g. Its precision and specific surface area are about 80 ~ 10100 times that of steel, and 50 ~ 70 times that of fly ash. Its precision will be relatively higher.
Finally, the particle material state and mineral phase structure, fire-resistant bricks in the composition process, because of the process of phase change by the utility of the surface pull, constitutes a non-crystalline phase amorphous round spherical particles. And the surface layer is quite slippery, some are more than one round spherical particles stick in a case of cheerful aggregates.
It is a kind of volcanic ash object with a very, very large specific surface area and very, very high activity. The material mixed with fire bricks, a fine spherical body can play a lubricating effect.
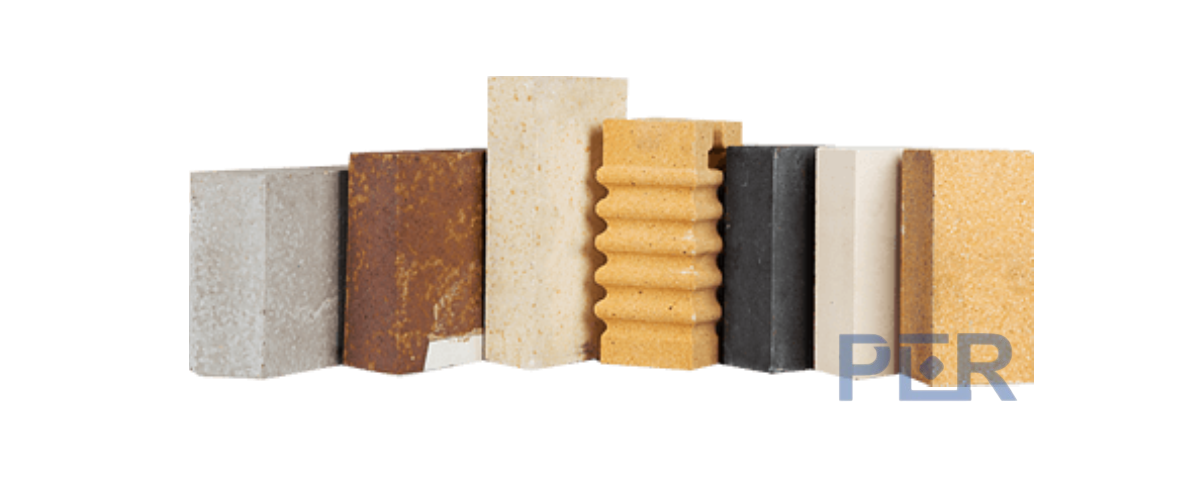
Refractory fire-resistant bricks can be used as high-temperature construction materials and structural materials for building kilns. As well as a variety of heating equipment that undergoes various physical and chemical changes and mechanical effects at high temperatures. Such as clay bricks, high alumina bricks, silicon bricks, magnesium bricks, silicon mullite bricks, etc.
High alumina bricks: High alumina refractory brick has more than 75% Al2O3 content and high refractories. It has a good ability to resist acid and alkali erosion. It is suitable for the location of the cement kiln firing zone.
Silicon carbide bricks: It has high-temperature resistance, low thermal expansion, good wear resistance, and good thermal shock resistance, and is suitable for kiln cooling belts and outlets.
Silica Mullite Bricks: The raw material is bauxite and silicon carbide, which is made by pressing and sintering. It is suitable for the transition zone with good thermal shock resistance, high strength, and good wear resistance.
Clay bricks: It is a weakly acidic refractory material. It has good thermal stability and is suitable for a hot air furnace chamber.
The Basic Properties Of Fire Bricks
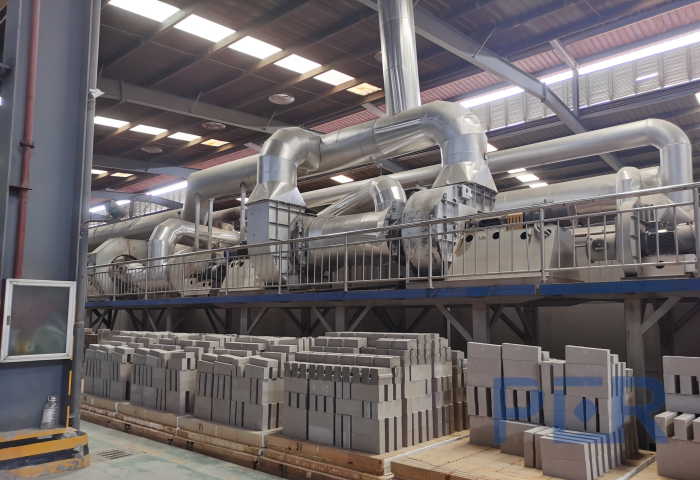
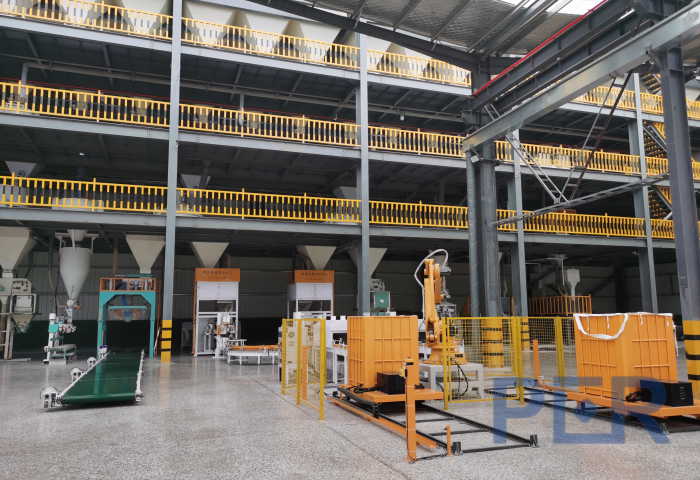
PER Refractory has more than 20 years of experience in the production of refractory bricks and refractory castables. Our rich experience ensures that our products have very much refractory material price advantage and quality advantage:
1. Load Softening Temperature Of Fire Bricks
“Refractoriness” refers to the refractory products in the production of the application process that can be resistant to a high-temperature degree, and not be melted function. The fire brick hydraulic press can effectively reduce the cost and save material loss.
Especially in the finished product rate has great progress, not only can make a refractory factory improve production efficiency, but also can greatly save labor costs.
The “room temperature resistance Zhuang strength” is one of the main quality indicators for the use of non-fired heat resistant fire bricks products with indefinite refractory materials.
2. Refractory Brick Pressure Resistance Strength
Small porosity of fire rated products, indicating a good degree of denseness, and the quality of the brick is good.
Apparent porosity is the ratio of the volume of pores (i.e., initiation of cavitation) to the total volume of fire-proof products within the atmosphere.
Firebrick products have two concepts of compressive strength.
One is called “room temperature compressive strength”, which is defined as the ultimate compressive stress strength in the indoor laboratory, according to the unit area of the specimen that can withstand without being destroyed.
The second is called “high-temperature compressive strength”, which is defined as the ultimate compressive stress that a refractory product specimen can withstand per unit cross-sectional area without being destroyed by firing to a specified high temperature. In refractory material, these two kinds of porosity are expressed in percentage.
3. Refractories Of Fire Refractory Bricks
The use of a four-column hydraulic system, pressing brick air force average, pressure, in the refractory industry than widely used.
Especially large refractories and special refractories production field, but also play an important role.
By changing the mold of the firebrick press, and material ratios, the production of a variety of special refractory materials becomes relatively easy.
Based on no increase in investment in equipment, refractory brick hydraulic presses can achieve a multi-purpose machine, a multi-purpose machine.
Another is called “true porosity”, that is, the volume of all the pores in the refractory products (including the open and closed pores) to the total volume of the ratio.
“Normal temperature pressure strength” for general refractory products, is a measure of its impact on the furnace material, wear, and liquid slag flushing can resist one of the important indicators.
4. Porosity
“High-temperature load softening point” refers to the fire resistant bricks for sale products in the production process, not only to resist high temperature, and to resist the slag, a variety of metal or material solutions, or processing parts of the flushing corrosion, acid-resistant bricks and withstand the pressure of the structural parts of the furnace body. Have the above function of the extreme limit called “high-temperature load softening point”.
There are also a few professional kilns on the refractory products porosity requirements should not be too small, to have the function of resistance to rapid cold and heat.
About PER Refractories Group
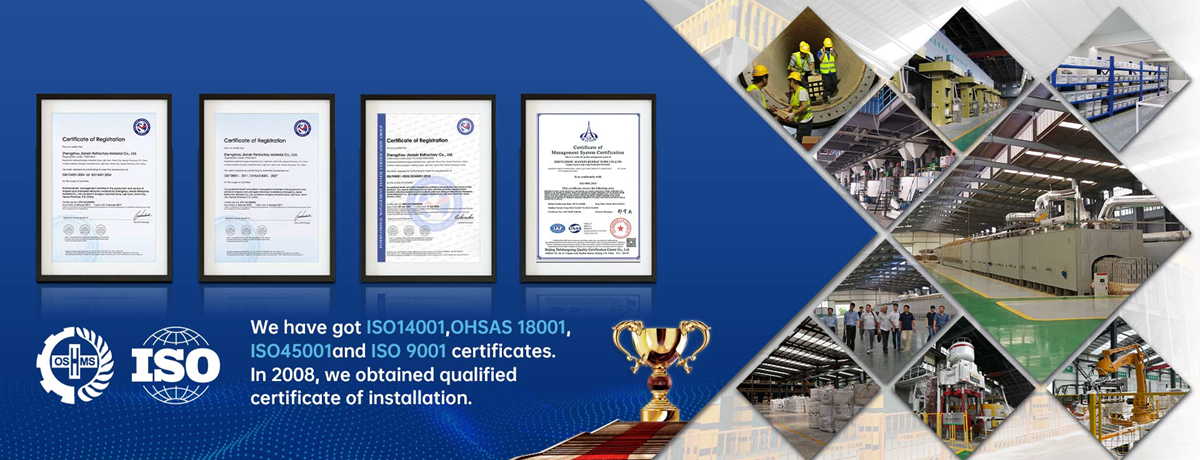
PER refractories Company is located in Xinmi City, Henan Province, the hometown of refractory materials in China. Our company is a technology-based refractory enterprise integrating R&D, production, sales, and technical service. The rich resources and excellent quality in the territory provide unparalleled superior conditions for the production of refractory materials. Our main firebrick for sales are refractory clay bricks, high alumina bricks, silica fire bricks, magnesium refractory bricks, mullite bricks, insulation fire bricks, and other high-temperature resistant products.
PER considers the most important thing, we believe in taking every product seriously and receiving every customer sincerely. To provide fast and high-quality results for all our customers. PER Refractories will be your most trustworthy refractory manufacturer and reliable partner.
Company PER refractory is the production base of green, energy-saving, and environment-friendly new refractory materials. Our company has passed ISO9001:2008 international quality system certification and GB/T24001-2004 / ISO14001:2004 environmental management system certification, enterprise-quality inspection agency certification. Our products are sold well in more than 20 countries all over the world. They are the preferred refractory products for metallurgy, non-ferrous, petrochemical, glass, ceramics, and other refractory industries.