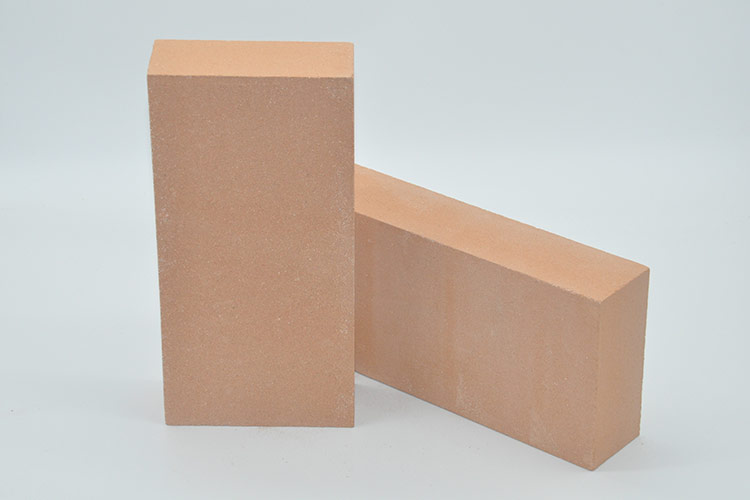
Batu bata tahan api are inorganic non-metallic materials with refractories of not less than 1580°C. Mereka adalah bahan dasar untuk menyajikan teknologi suhu tinggi, bahan struktural untuk tungku batu dan peralatan termal lainnya, and the functional materials for manufacturing certain high-temperature containers and parts or playing special roles.
The successful use of refractory firebricks under the action of high temperature must have a good organizational structure, sifat termal, peralatan mekanis, and use properties. That is a high degree of refractories, suhu pelunakan beban, ketahanan guncangan termal, dan ketahanan terhadap erosi kimia dan sifat lainnya. This can withstand a variety of physical and chemical changes to meet the requirements of the use of thermal equipment and components.
Then there is a question, refractory bricks can be high-temperature resistant? Why can’t other materials withstand high temperatures? PER refractory team will give you a detailed answer.
1. From The Raw Material Analysis
Refractory brick manufacturing raw materials are generally natural ores, such as bauxite, silika, magnesite, and other raw materials are processed and manufactured from different properties of refractory bricks, such as aluminum and silicon refractory bricks, batu bata tahan api silika, and magnesia refractory bricks three types.
When bauxite is chosen as the raw material for the production of alumina-silica refractory bricks, its main component is alumina. It is hydrated alumina containing impurities, an earthy mineral, insoluble in water, soluble in sulfuric acid, and sodium hydroxide solution.
The main use is for aluminum refining, and making refractory materials, because the refractories of high alumina bauxite clinker is up to 1780℃, with strong chemical stability and good physical properties.
The bauxite is purified at high temperature to produce a corundum main crystal phase with alumina content greater than 90% can produce ultra-high temperature refractory bricks electrofused zirconium corundum bricks.
The raw material for making silica refractory bricks is silica main component is SiO2 which is the higher the content, the higher the refractories. The most harmful impurities are AL2O3, K2O, Na2o, dll..
Itu production of silica bricks is made of natural silica as raw material, plus an appropriate amount of mineralizing agent to promote the conversion of quartz in the billet into, scaled quartz. It is slowly fired by 1350~1430℃ under a reducing atmosphere. Has high high-temperature strength. The load softening temperature is at 1620℃.
Magnesite is the main raw material for making magnesia refractory bricks, its basic composition is MgO, magnesium oxide has high refractory insulating properties.
It can be transformed into a crystal by high-temperature sintering above 1000℃, and it will become sintered magnesite sand when it rises to 1500-2000℃. Then it can be made into magnesium bricks or magnesium pounding material after crushing to a certain size or powder.
Magnesia refractory bricks belong to alkaline refractory bricks, have strong resistance to alkaline slag, but can not resist the erosion of acid slag, refractories in 2000 ℃ atau lebih, but its load softening point is only 1500 ℃, thermal shock stability is poor.
2. Belong To Inorganic Non-Metallic Materials
Inorganic non-metallic materials and organic polymer materials and metal materials are listed as the three major materials.
Ordinary inorganic sub-metallic materials are characterized by high compressive strength, kekerasan tinggi, ketahanan terhadap suhu tinggi, and corrosion resistance.
Selain itu, ceramics have excellent characteristics in corrosion resistance and refractory materials in heat and thermal insulation properties.
These are for metal materials and polymer materials can not be compared.
Namun, compared with metal materials, it has low fracture strength and lacks ductility.
Compared with polymer materials, the manufacturing process is complicated because of its higher density.
3. Forming And Sintering
The refractory brick production process is through the process of mineral crushing—raw material mixing—mechanism forming—high-temperature sintering. The final output is a product that resists high temperatures.
The billet in the high-temperature tunnel kiln sintering temperature will be higher than its product load softening temperature, the general sintering temperature of 1500 ℃ atau lebih. The fire resistance is above 1770℃. The resistance to high temperature is better. Refractory bricks are mainly used for the masonry of steel-making electric furnaces, glass melting furnaces, cement rotary furnaces, and other kiln linings.
Summary
Refractory brick can resist high temperature for three reasons mainly relying on
1. The high refractories of the raw minerals used in refractory bricks.
2. Sebagai bahan anorganik nonlogam dari tingkat bahan bakunya menentukan tingkat kegunaannya.
3. The finished billets are subjected to high temperatures of over 1500°c in high-temperature tunnel kilns.
So refractory bricks can resist high temperatures suitable for high-temperature kiln lining.