Magnesia Brick
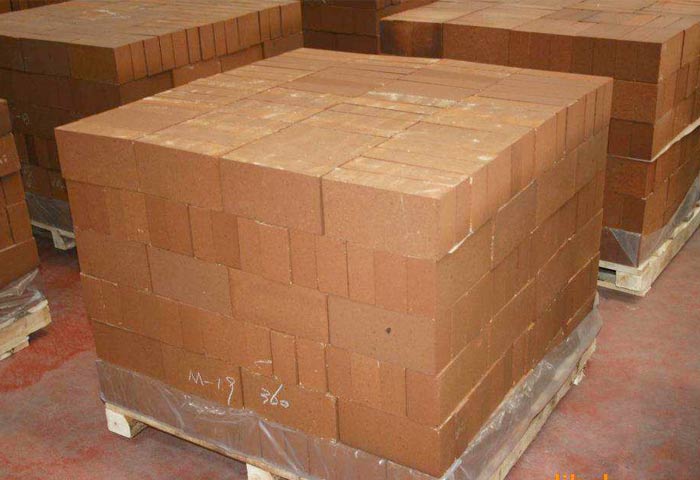
Magnesia refractory brick is a refractory material with magnesite, seawater magnesia sand, and dolomite as raw materials, magnesite as the main crystalline phase, and magnesium oxide content above 80%.
It is an alkaline refractory material. Magnesia refractory material is one of the widely used auxiliary materials in the metallurgical industry because of its high refractory performance, high-temperature strength, and resistance to alkaline slag leaching.
The load softening point and thermal shock resistance of high purity magnesia bricks are much better than the general magnesia bricks. High refractories, good resistance to alkaline slag, and iron slag are important high-grade refractory materials.
PER company, as a professional refractory brick manufacturer in China, can provide you with lower prices than the market. Contact us now to get the latest price list of magnesia refractory bricks.
Types And Characteristics Of Magnesia Refractory Bricks
Magnesia refractory brick products are mostly produced by the sintering method, the firing temperature is generally between 1500~1800℃, in addition, a chemical bonding agent can also be added to make non-burning bricks and indefinite refractory materials. PER refractory magnesia bricks mainly used in flat furnaces, electric furnaces, oxidation converters, non-ferrous metal smelting furnaces, cement kilns, alkaline refractory calcining kilns, etc.
These products can be divided into two categories: metallurgical magnesia and magnesia products. According to the chemical composition and use can be divided into metallurgical magnesium sand, magnesium bricks, magnesium silicon bricks, magnesium aluminum bricks, magnesium calcium bricks, magnesium carbon bricks, and other varieties. Its performance is greatly affected by the CaO/SiO2 ratio and impurities.
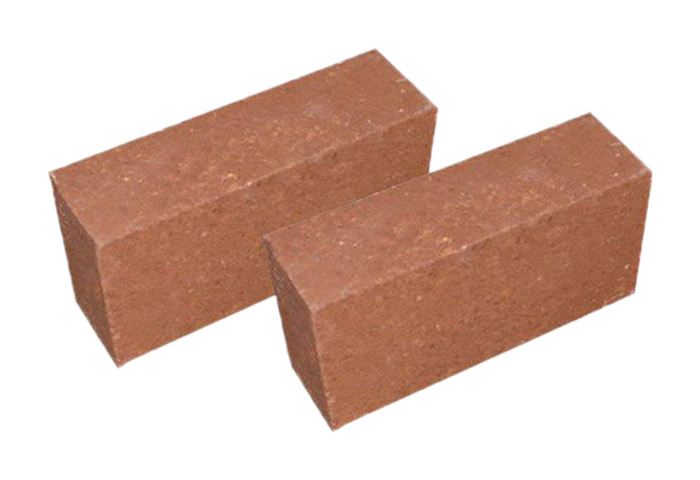
Magnesium Brick
The most important brick in alkaline refractories, is high refractoriness, good resistance to erosion of iron oxides, alkaline slag, and high calcium melt.
Magnesium brick has fired magnesium brick and not burned magnesium brick, fired magnesium brick firing temperature is generally 1550-1600 ℃, high purity brick firing temperature of 1750 ℃, or even higher.
Magnesium bricks are widely used in steelmaking furnace linings, ferroalloy furnaces, iron mixing furnaces, non-ferrous metallurgical industrial furnaces, lime kilns, tunnel kilns and so on in the iron and steel industry.
Magnesium Carbon Brick
Magnesia carbon brick is made of high melting point alkaline oxide magnesium oxide (melting point 2800℃) and high melting point carbon material which is difficult to be infiltrated by slag as raw material. Add a variety of non-oxide additives, with carbon binding agents combined from the non-burning carbon composite refractories.
Magnesium-carbon bricks are mainly used for the inner lining of the converter, AC arc furnace, DC arc furnace, slag line of ladle, and other parts. Magnesium carbon brick as a composite refractory material, effective use of magnesium sand slag erosion resistance, and carbon’s high thermal conductivity and low expansion compensate for the magnesium sand spalling resistance of the biggest shortcomings.
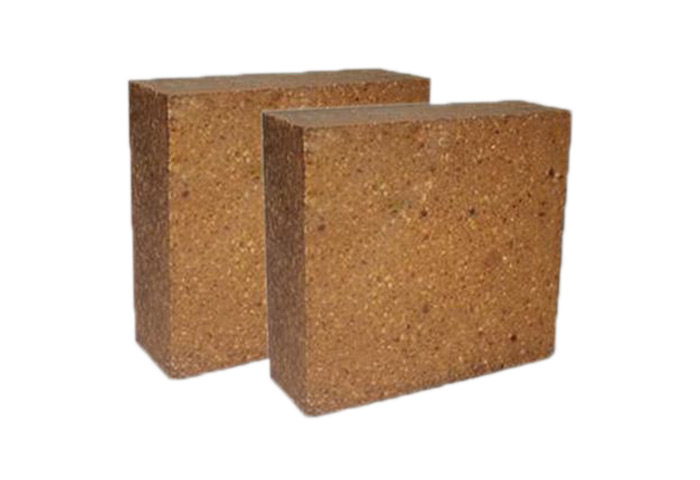
Magnesium-Aluminum Brick
Compared with magnesium brick, magnesium aluminum brick has good resistance to rapid freezing and rapid heating and can withstand water cooling 2025 times, or even more times, which is the outstanding advantage of magnesium aluminum brick.
The refractoriness of magnesium-aluminum bricks is more than 2000℃, the performance of resistance to rapid cooling and heating is better than magnesium bricks, and it can resist the erosion of alkaline slag. It is used to build the roofs of alkaline flat furnaces and electric furnaces for steel making.
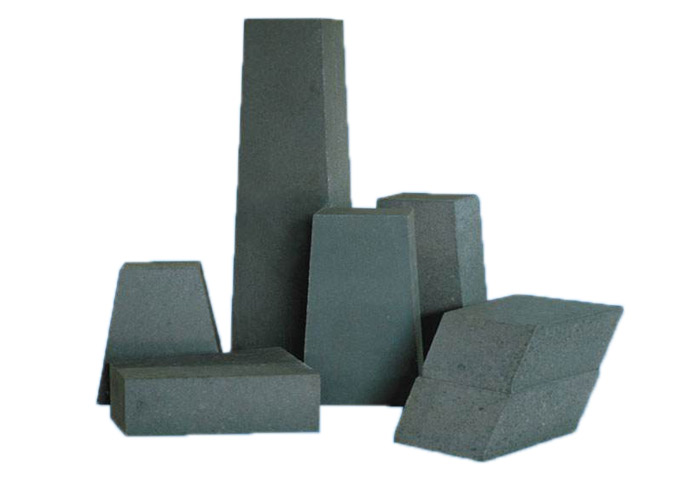
Magnesium Calcium Brick
Magnesite is the main mineral composition, with tricalcium silicate and dicalcium silicate as a combination.
In addition to poor thermal shock stability, other performance indicators than magnesium brick are superior.
Magnesium-calcium bricks are mainly used as the lining of AOD furnace for smelting stainless steel and the cladding of VOD ladle. Replacing the original magnesium-chromium brick, it is the most important magnesium-calcium refractory material.
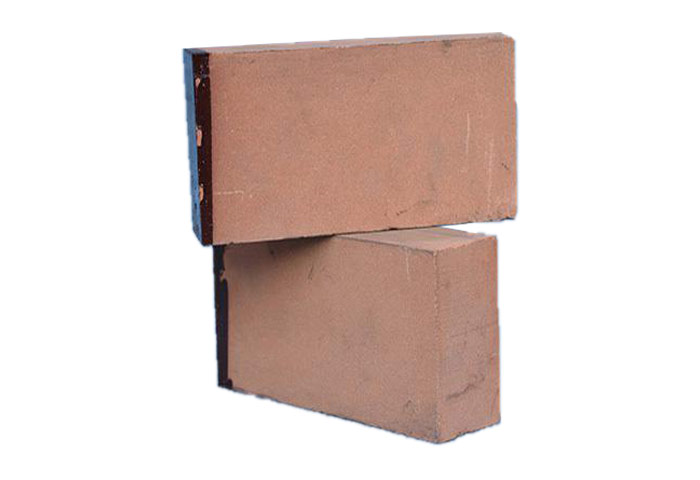
Magnesium Silicon Brick
Square magnesite is the main mineral composition, with magnesia olivine as a matrix bond.
Its performance and magnesium brick are roughly the same.
But the load softening temperature is higher than magnesium brick, and slag resistance is also better.
Magnesium-silica bricks are mainly used in steel rolling furnace, heating furnace bottom, but also used as glass kiln heat storage room lattice brick, etc.
Technical Index
Product performance | Alumina magnesia carbon brick | Magnesia aluminum carbon brick | Magnesia carbon brick | ||||
chemical composition (%)≥ | AL2O3 | 65 | 70 | 10 | 15 | ||
Mg0 | 15 | 10 | 75 | 70 | 78 | 74 | |
C | 7 | 7 | 10 | 8 | 10 | 14 | |
Apparent porosity(%) ≤ | 5 | 5 | 3 | 3 | 3 | 3 | |
Bulk density (g/cm³)≥ | 3 | 3 | 3 | 3 | 3 | 2.9 | |
Normal temperature compressive strength (MPa)≥ | 40 | 40 | 40 | 40 | 40 | 40 | |
High temperature flexural strength(MPa)≥(1400℃×0.5h) | 6 | 6 | 7 | 7 | 6 | 8 | |
Application | molten pool, bottom of ladle | molten pool | slag line |
The Difference Between High Alumina Brick And Magnesium Brick
High alumina brick is a series of aluminum and silicon products, and magnesium brick is a series of magnesium products.
High alumina brick can resist weak alkali and weak acid atmosphere and is a neutral product. Magnesium brick resists strong alkali erosion, cannot be used in an acid atmosphere and belongs to alkaline series products.
High alumina brick and magnesium bricks are two different materials and the nature of refractory products, magnesium brick density is above 3.0, melting point at 2850℃, high alumina brick density is above 2.3, melting point at 1500℃.
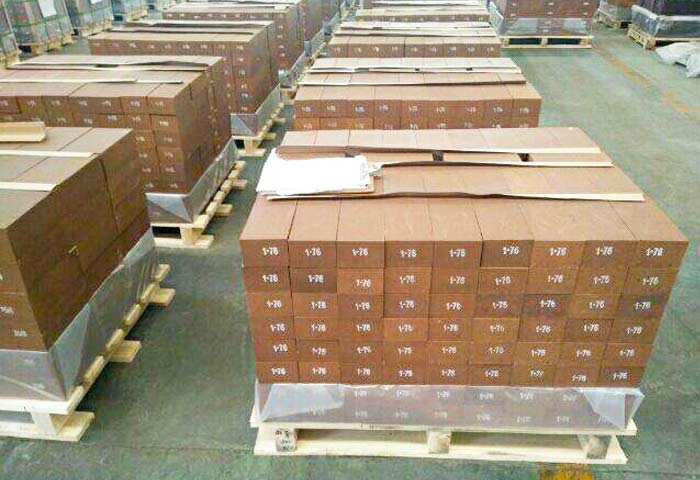
Magnesium Bricks
1. The refractories of magnesium brick is more than 2000℃, and the load soft is at 1800℃.
2. But magnesium brick has high thermal conductivity, poor thermal shock resistance, and a high degree of heat resistance.
3. Magnesium brick's resistance to acidic slag is poor, and can not directly contact acidic products.
4. If the acid is in the kiln lining, use high alumina brick will be separated from it to use.
5. And the magnesium brick's resistance to hydration is poor, easy to meet the water long white hair, but also produces cracks, strength reduced.
6. Magnesium brick in storage and transportation during all to prevent moisture, rain, and snow.
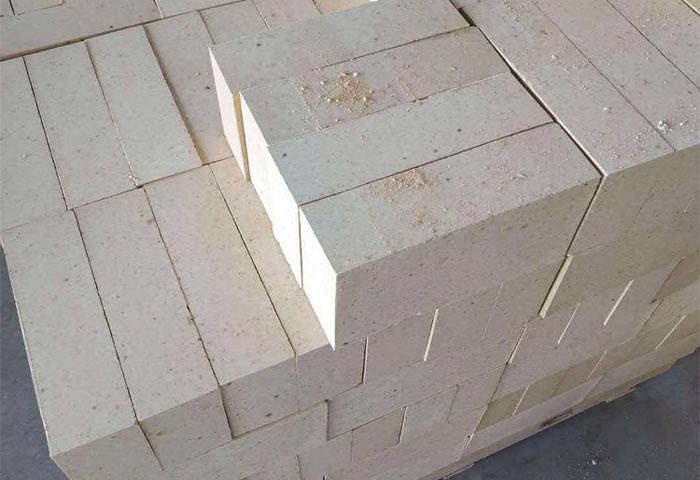
High Alumina Bricks
1. The refractories of high alumina brick are above 1700℃.
2. Load softening temperature at 1520 ℃, the highest does not exceed 1600 ℃.
3. The load softening temperature of high alumina brick is also very different according to different grades of raw materials.
4. The third-grade high alumina brick load softening temperature is also at 1410℃ or so.
5. Although high alumina brick is neutral brick, thermal shock stability is good, not afraid of hydration, and can be used in weak alkali, weak acidic atmosphere.
Summarize
So in different kiln linings of different temperatures, the choice of magnesium brick or high alumina brick is according to the degree of erosion and atmosphere selected. The alkaline atmosphere must choose magnesium brick. Using a temperature below 1400 ℃, weak alkali or weak acid atmosphere can choose high alumina brick.
The difference between high alumina brick and magnesium brick is that the material is different, the use temperature is different, the erosion-resistant atmosphere is different, and the thermal shock effect is different. Another difference is the market price, high alumina brick price is low, and magnesium brick price is high. Of course, as a professional refractory material supplier with many years of manufacturing and exporting experience, we can offer you a lower price than the market price.
About PER Refractories Company
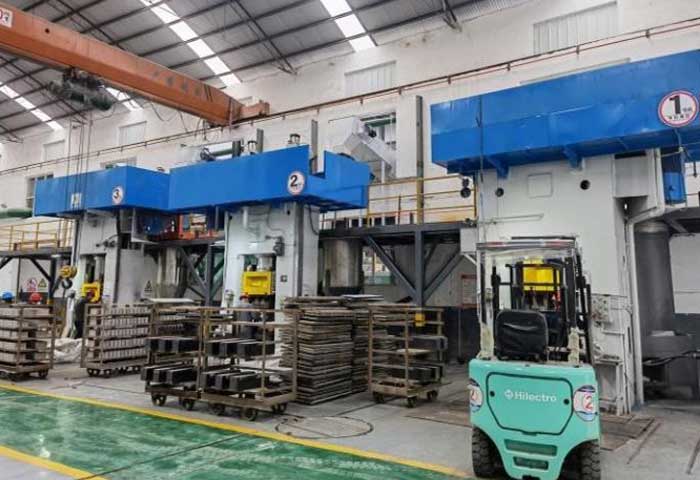
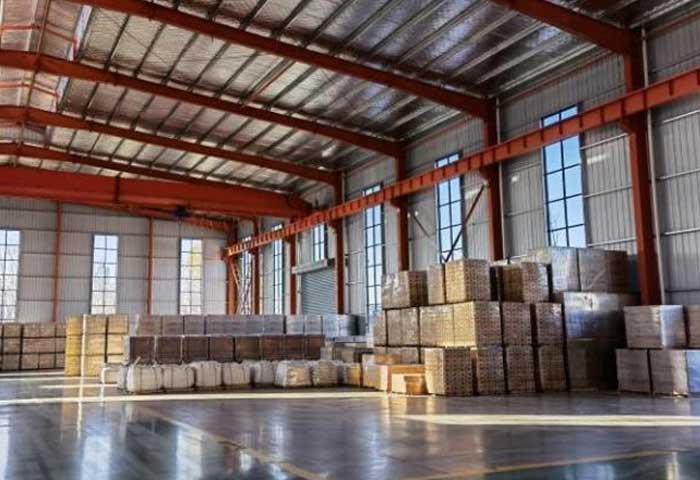
PER refractories Company is located in Xinmi City, Henan Province, the hometown of refractory materials in China. Our company is a technology-based refractory enterprise integrating R&D, production, sales, and technical service. The rich resources and excellent quality in the territory provide unparalleled superior conditions for the production of refractory materials. Our main products are refractory clay bricks, high alumina refractory bricks, silica refractory bricks, magnesium refractory bricks, mullite bricks, insulation bricks, and other high-temperature resistant products.
Company PER refractory is the production base of green, energy-saving, and environment-friendly new refractory materials. Our company has passed ISO9001:2008 international quality system certification and GB/T24001-2004 / ISO14001:2004 environmental management system certification, enterprise-quality inspection agency certification. Our products are sold well in more than 20 countries all over the world. They are the preferred refractory products for metallurgy, non-ferrous, petrochemical, glass, ceramics, and other refractory industries.