1100 Graus de tijolo refratário é o que é tijolo de fogo?
Muitos tijolos refratários encontram-se 1100 graus, tijolos de barro baratos, bons tijolos com alto teor de alumina, tijolos de mulita, tijolos de sílica tijolos de magnésio, expensive electrofusion bricks, etc., the choice of refractory brick temperature is only an indicator, but also according to the working conditions, environment, operating characteristics, etc. to choose.
According to the definition of refractory refractoriness greater than 1580 degrees inorganic non-metallic materials and products. Refractoriness refers to the temperature at which the material reaches a specific degree of softening under the action of high temperature, which marks the performance of the material to resist the action of high temperature. Refractory bricks need to withstand very high temperatures, and people also need them to work properly even at high temperatures.
Portanto, in the unit volume weight, the density is high, so that can indicate that the denseness of the refractory brick is good, and the strength it brings may be high. Refractory bricks also have higher requirements for their porosity of them.
No entanto, today people need to do specific requirements in the process of industrial production, but a manufacturer must strictly control the apparent porosity has a very high quality.
Por outro lado, the thermal shock resistance of this material is very good, it is resistant to rapid changes in temperature without being destroyed.
Portanto, it can be concluded that refractory bricks have unit volume weight, alta densidade, good denseness, força elevada, e outras características.
Common Refractory Bricks
1. Silica-aluminum refractory bricks. It is known that it is based on the basic theory of the AL2O3/SiO2 binary system phase diagram, incluindo principalmente os seguintes.
2. Tijolos de sílica. Silica brick refers to the refractory brick containing SiO293% or more, which is the main variety of acid refractory brick. É usado principalmente para fornos de coque de alvenaria, mas também usado em uma variedade de vidro, cerâmica, calcinador de carbono, refractory bricks for the vault of the hot work kiln, and other load-bearing parts, in the hot air furnace of high-temperature load-bearing parts also used, but should not be used in the hot work equipment below 600 ℃ and temperature fluctuations.
3. Tijolos de argila. Clay bricks are mainly composed of mullite (25% para 50%), fase de vidro (25% para 60%), e quartzo quadrado e quartzo (até 30%).
Geralmente, hard clay is used as raw material, pre-calcined to mature material, then with soft clay, shaped by semi-dry or plastic method, and fired at 1300-1400 C to make clay brick products. Can also add a small amount of water glass, cimento, and other binding agents made of non-fired products and indefinite materials.
It is commonly used refractory bricks in blast furnaces, fornos de ar quente, fornos de aquecimento, caldeiras de energia, fornos de cal, fornos rotativos, fornos de vidro, cerâmica, e fornos de queima de tijolos refratários.
4. Tijolo de alta alumina. The mineral composition of high alumina bricks is corundum, mulita, e fase de vidro. Its content depends on the AL2O3 / SiO2 ratio and the type and number of impurities, the grade of refractory bricks can be classified according to the AL2O3 content.
The raw materials are natural ores of high alumina bauxite and silica line type, also mixed with electrofused corundum, sintered alumina, mulita sintética, and clinker calcined with alumina and clay in different proportions. It is mostly produced by the sintering method.
But the products also have fused cast bricks, tijolos granulados fundidos, tijolos crus, e tijolos refratários sem forma. High alumina bricks are widely used in the steel industry, indústria de metais não ferrosos, e outras indústrias.
5. Corundum refractory brick, corundum brick refers to AL2O3 content of not less than 90%, corundum as the main phase of a refractory brick, can be divided into sintered corundum brick and electrofusion corundum brick.
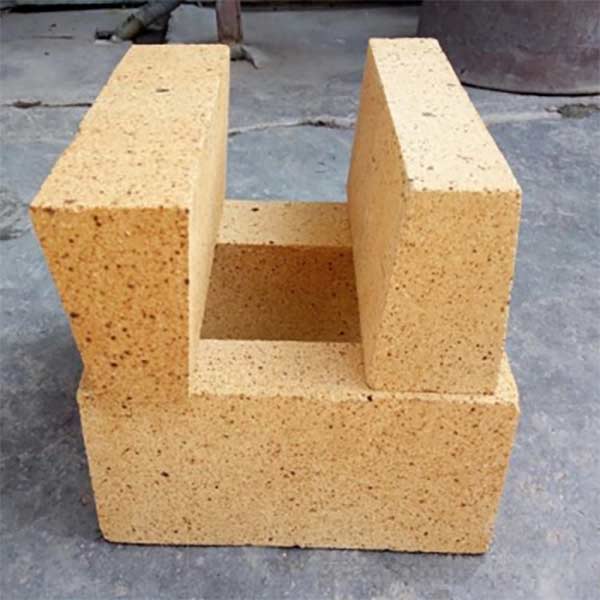
What Are The Performance Requirements Of Refractory Bricks?
1. Porosidade
The porosity in the refractory brick includes open and closed porosity. Porosity generally refers to the volume of the visible pores within the atmosphere and the percentage of the total volume of the product, also called visible porosity. The smaller the porosity of the product, the better the thermal conductivity and the higher the compressive strength, but the resistance to rapid cold and heat is poor.
2. Bulk Density And True Density
Bulk density is the number of mass per cubic meter of brick including all the porosity, while the volume of the brick sample includes only the rock part when calculating the true density. Since the true density of different crystalline quartz is not the same, portanto, the true density of the brick can understand its firing situation. The true density is smaller for better-fired silica bricks.
3. Room Temperature Compressive Strength
Products at room temperature unit area can withstand large pressure, called room temperature compressive strength. The structure is uniform and dense, and the products with good firing have high room temperature compressive strength.
4. Thermal Expansion
Usually expressed by the average linear expansion rate in a certain temperature range.
5. Condutividade térmica
Refers to the performance of refractory bricks to transfer heat. It is expressed in terms of thermal conductivity, and its unit. Baixa porosidade, dense structure of the brick, and thermal conductivity are good. The crystalline structure has better thermal conductivity than the glassy one. Most refractory bricks such as silica bricks and clay bricks thermal conductivity, with the increase in temperature, but there are a few refractory bricks (such as magnesium bricks and silicon carbide) with thermal conductivity, but with the temperature increases and decreases.
6. Fire Resistance
Fire resistance indicates that the refractory bricks at high temperatures tosist softening (melting) performance, which refers to the temperature when the top of the refractory cone specimen bent down and touch the side of the chassis.
7. Temperatura de amolecimento de carga
Indicates the ability of the refractory brick to resist temperature under a certain load. Load softening temperature is the specimen under 0.2MPa pressure, heated at a certain rate of heating, as the temperature increases, the specimen continues to produce deformation, hen the large height of the specimen is reduced by 0.6% of the temperature, isso é, the load softening temperature. It is related to the chemical properties of refractory bricks, crystalline structure characteristics, the viscosity of the glass phase at a certain temperature, the relative ratio of the crystalline phase to the glass phase, firing temperature, and particle size composition.
8. High-Temperature Volume Stability
Firebrick and refractory bricks in long-term use at high temperatures, the volume of irreversible changes in performance, usually residual expansion (or shrinkage) to indicate the volume stability of refractory bricks. Its specific indicators are refractory bricks at a certain temperature, heating at a certain time, after natural cooling, measuring its volume change, and the value of the percentage of the original volume, known as residual expansion (or residual shrinkage).
9. Thermal Stability
Refractory brick resistance to rapid changes in temperature without damage. The test method is to put half of the specimen in the heating furnace, the other half outside the furnace, heated to 850C when holding 40 minutes, and then put into the flow of cooling water tank in the rapid cooling, so repeatedly, when the damage off part of the mass of the original specimen for 20% of the mass of the rapid cooling and rapid heating times. It is closely related to the size of the expansion coefficient of the product, the unevenness of the internal temperature distribution of the product, and the shape and size of the product.
10. Resistance To Erosion
Refractory brick at high temperatures to resist the chemical and physical effects of slag, furnace decomposition products performance. The main factors affecting the resistance to erosion are the chemical composition of the product and slag, working temperature, the nature of the decomposition products of the furnace charge, and the density of the product.
What Kind Of Bricks Are 1100-Degree Refractory Bricks?
According to the definition of refractory materials, refractory bricks are shaped refractory materials, ordinary refractory products can meet the high-temperature requirements of 1100, if the refractory clay bricks can meet the requirements of use do not use high alumina bricks.
Refractory Material Cracking, Shedding, Easy To Wear How To Do?
If you want to solve the problem completely, you need to dig from the root cause and analyze the real reason. per refractory is engaged in the production of refractory materials, research, and development services for many years, can solve all kinds of difficult problems of high-temperature furnace lining, welcome new and old friends to consult and technical exchanges.